Exploring Lost Wax Casting in Gemstone Artistry
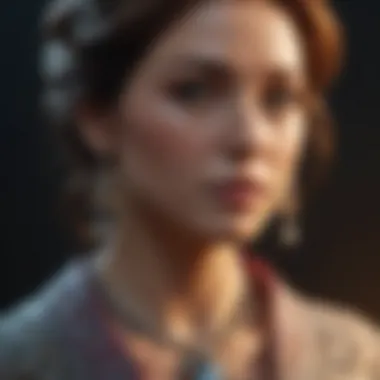
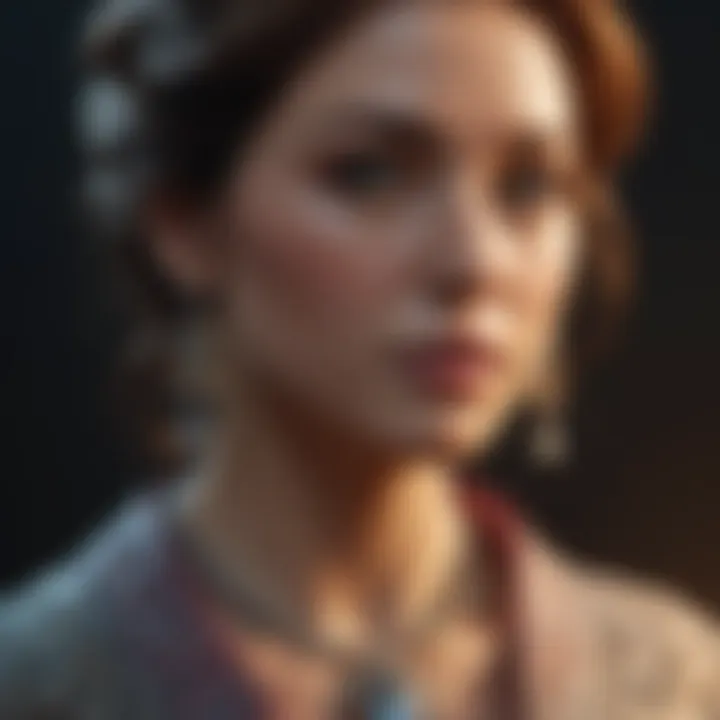
Intro
Lost wax casting, a time-honored technique, holds a treasured place in the world of gemstone artistry. This process combines advanced craftsmanship with artistic expression, allowing creators to transform raw materials into unique works of art. Understanding this method is essential for those interested in jewelry making, gemstone collection, or artistic sculpture.
The exploration of lost wax casting in the context of gemstones reveals not only the technical process involved but also sheds light on the vibrant history and innovative materials tied to it. Jewelers aiming to create bespoke pieces can learn significantly from mastering the intricacies of this method.
This article aims to provide a comprehensive look at the significance of lost wax casting molds, the various materials utilized, and the modern techniques that are shaping the field.
Gemstone Overview
Description of the Gemstone
Gemstones have long captured human imagination. They are not merely ornamental; they carry meanings, possess histories, and serve as a canvas for artistic expression. Each gemstone differs in color, structure, and clarity, contributing to its overall value and appeal.
The lost wax casting technique allows for intricate designs and detailed inclusions to be represented in metalwork, amplifying the beauty of the gemstone used within it. High-quality gemstones like diamonds, emeralds, and sapphires are often the stars of these pieces, showcasing their brilliance in unique forms.
Physical Properties
Gemstones exhibit various physical properties, which can impact their use in jewelry making. These properties include hardness, specific gravity, refractive index, and cleavage. Understanding these attributes can help artists and collectors make informed decisions on which gemstones complement specific designs.
- Hardness: A measure of resistance to scratching. Diamonds rank highest on the Mohs scale.
- Specific Gravity: Indicates the density of the gemstone. This is crucial when determining both quality and value.
- Refractive Index: Measures how much light is bent when entering the gemstone, affecting its sparkle.
- Cleavage: Describes how a gem breaks along certain lines. This plays a role in how it can be set or shaped.
Healing Properties
Metaphysical Attributes
Many gemstone enthusiasts believe in the healing properties of gemstones. Each type of gemstone is thought to carry specific energies or vibrations. For instance, amethyst is said to promote calmness, while rose quartz is associated with love and emotional healing.
Common Uses in Holistic Practices
In holistic practices, gemstones serve as tools for meditation and energy work. They are often used in:
- Crystal healing therapies
- Chakra balancing sessions
- Feng Shui applications
"Gemstones are not just for aesthetic pleasure; they encompass deeper meanings and healing properties for those open to their energies."
The integration of lost wax casting transcends the simple creation of objects. It fosters a dialogue between the artist and the material, resulting in pieces that are both beautiful and meaningful.
This article will further delve into the mechanics of lost wax casting and its practical implications for gemstone artists, expanding the understanding of this exquisite craft.
Intro to Lost Wax Casting
Lost wax casting stands as a pivotal technique in the realm of gemstone artwork, merging ancient tradition with modern craftsmanship. The significance of this method lies not only in its historical roots but in its capacity to produce intricate and detailed pieces that are highly sought after in the jewelry market. By understanding lost wax casting, artisans and hobbyists alike can appreciate the technical skill and artistry involved in creating unique jewelry and sculpture.
Through this article, we will deeply explore lost wax casting molds, examining their role in gemstone artwork. This section will lay the groundwork by defining the process and providing a historical context. Such knowledge is essential for anyone looking to engage with this sophisticated art form and enhance their work or collection.
Definition and Overview
Lost wax casting, also known as investment casting, involves the creation of a wax model which is later encased in a mold. The wax is melted away, leaving a cavity that retains the exact shape of the original model. Subsequently, molten metal or resin is poured into this mold to create the final object. This technique allows for high precision in reproducing details, making it favored by artisans creating intricate jewelry designs or complex sculpture.
Historical Context
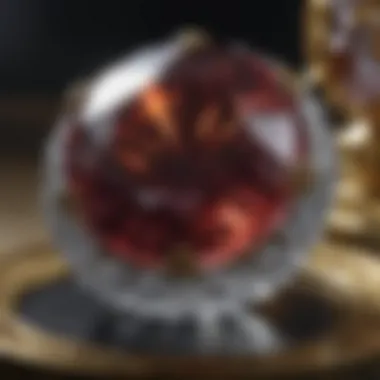
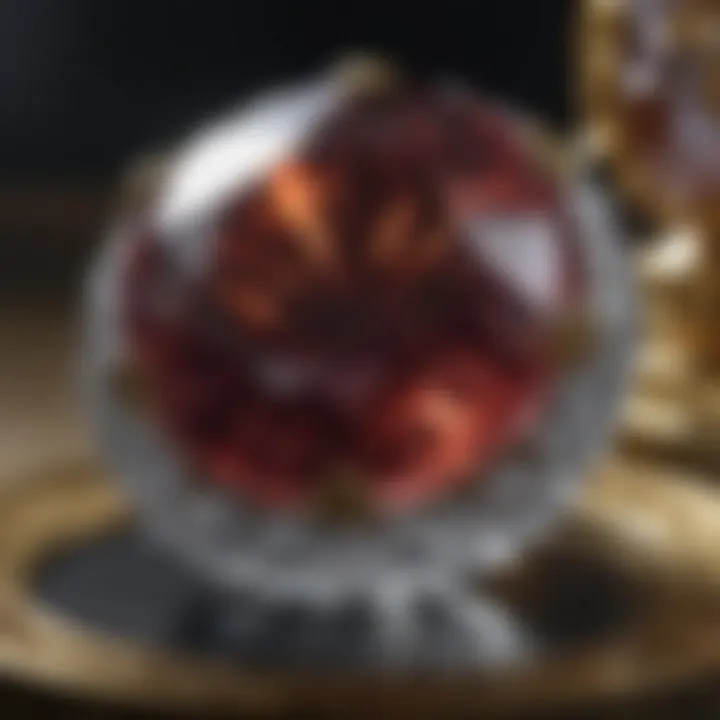
The origins of lost wax casting trace back thousands of years, with evidence found in ancient civilizations such as the Egyptians, Greeks, and Chinese. In Egypt, the method was employed to create delicate figurines and jewelry, while in Greece, it was used for producing coins and religious artifacts. Over time, this technique evolved and spread, influencing various cultures and methodologies. Today, it continues to be a critical process in both industrial applications and fine arts.
Understanding this history affords contemporary artists and collectors an appreciation for the craftsmanship involved in lost wax casting. The revival of this technique in modern artwork reaffirms its value, bridging ancient practices with contemporary designs.
Materials Used in Lost Wax Casting
The materials utilized in lost wax casting are crucial to the effectiveness and quality of the finished gemstone artwork. Understanding these materials allows artists to make informed choices, ensuring their creations meet both artistic and functional standards. There are two primary components to scrutinize: wax variants and their properties, alongside mold composition.
Wax Variants and Their Properties
Wax serves as the foundational material in the lost wax casting process. Various types of wax are available, each with its own characteristics and benefits. The choice of wax can significantly influence the details and overall quality of the final product.
- Paraffin Wax: Widely used due to its affordability and ease of use. It is also compatible with various molding techniques, although its melting point may vary.
- Beeswax: Highly regarded for its smooth texture and natural properties. It melts at lower temperatures, making it easier to manipulate. Artists often prefer beeswax for detailed work, as it allows for finer finishing.
- Synthetic Waxes: These are engineered for specific applications. They offer more control over melting points and burning characteristics, making them ideal for complex designs.
- Negative and Positive Waxes: Negative wax is used for creating detailed impressions, while positive wax stands out for building molds. Knowing when to use each type can enhance the precision of the final casting.
The right wax can lead to better detail retention and a smoother surface finish in the gemstone art. However, selection often depends on the artist's specific needs and the complexity of the piece being created.
Mold Composition
The composition of molds in lost wax casting has a direct effect on the casting process and the quality of the final sculpture or jewelry piece. Molds are often made from materials such as ceramics, metals, or even newer composite materials, each bringing unique properties to the table.
- Ceramic Molds: These are traditionally used in lost wax casting. They are capable of withstanding higher temperatures, making them suitable for a variety of metals. Their porous nature allows for gas escape, which is crucial during the melting process.
- Metal Molds: Utilized for mass production, metal molds allow for quicker turnarounds. They offer greater durability but generally restrict the intricacy that can be achieved compared to ceramics.
- Composite Molds: These are gaining popularity due to their balance of durability and flexibility. They can incorporate advanced materials that support high-temperature applications while providing detailed impressions.
The choice of mold composition impacts not just the details and finish of the artwork but also its durability. Artists should carefully consider how different materials respond to heat and pressure to achieve the desired effect.
The interplay between wax type and mold material must not be underestimated. Each selection plays a pivotal role in the final outcome of the lost wax casting process.
The Lost Wax Casting Process
The lost wax casting process is a hallmark technique in creating gemstone artwork. It plays a crucial role in shaping the unique forms that characterize this art. Understanding this process provides insight into the technical mastery required for exquisite craftsmanship. The methods employed directly influence the final aesthetic and functional quality of the pieces produced.
Creating the Wax Model
The first step in the lost wax casting process is creating a precise wax model. Artists often sculpt this model by hand or use machines for greater accuracy. The choice of wax is essential, as different types can affect the details that can be captured. Typically, soft wax is used for easy carving, while harder variants help in retaining shape during mold-making.
Once the model is prepared, it serves as the template for the final piece. This stage is pivotal since defects in the wax may carry over to the final casting. Precision in this phase ensures that the intricate designs envisioned by the artist manifest accurately in gemstones. Additionally, wax models can be remade easily, offering flexibility to artists during the design process.
Mold Making Techniques
After the wax model is complete, the next phase involves the creation of a mold. There are several techniques to achieve this, but two common methods include:
- Investment Casting: This method involves encasing the wax model in a heat-resistant material. Once set, the mold is heated to remove the wax, leaving a cavity for casting. This process is advantageous for capturing fine details.
- Silicone Molds: Silicone can also be used to create flexible molds. This is often preferred for designs that require multiple reproductions, as the flexibility allows for easier removal of the finished casting.
Choosing the right mold-making technique depends largely on the complexity of the design and the intended material for the final piece. Each method has its trade-offs, with investment casting often preferred for single unique works, and silicone molds for replication.
Casting and Cooling
The casting phase is where the actual transformation occurs. Molten metal or resin is poured into the prepared mold, filling the space left by the removed wax model. Heat plays a critical role during this stage, as it not only shapes the material but also influences its structural integrity and surface finish. Additionally, proper venting must be ensured, allowing gases to escape to avoid imperfections.
Once the metal has cooled and solidified, the mold is removed. This process reveals the final piece, ready for any additional finishing touches. Cooling must be monitored carefully, as improper cooling can lead to warping or cracking. This phase finalizes the rigorous work initiated in the wax model and mold-making stages, showcasing the artisans' skills.
"Attention to detail during the lost wax casting process can significantly enhance the quality and uniqueness of the finished piece."
Applications of Lost Wax Casting in Gemstone Art
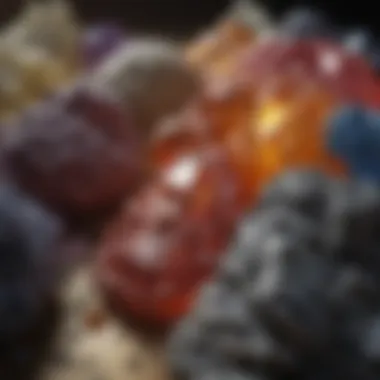
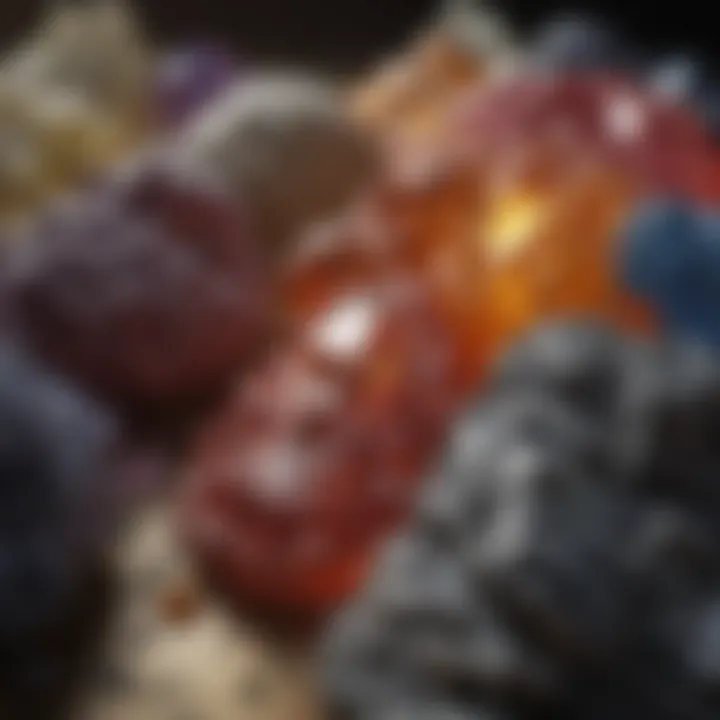
Lost wax casting plays a significant role in the realm of gemstone art. It allows artisans to transform raw materials into intricate pieces of jewelry and stunning sculptures. This technique provides a high degree of detail and design flexibility, making it indispensable for artists eager to push the boundaries of creativity. Additionally, it enables the incorporation of gemstones in unique ways, enhancing both aesthetic appeal and value. Understanding these applications provides insight into the versatility and importance of lost wax casting in gemstone artwork.
Jewelry Production
Types of Jewelry
Jewelry produced through lost wax casting includes various forms such as rings, necklaces, bracelets, and earrings. Each type presents unique characteristics that enhance the artistry and craftsmanship. One key feature of cast jewelry is the ability to reproduce complex designs with high precision. This makes lost wax casting a preferred method for creating intricate patterns and textures that would be difficult to achieve by other means. For instance, statement pieces such as elaborately carved pendants showcase both the artistry involved and the suitability of this method for creating standout jewelry. However, precision also demands careful planning, as mistakes in the initial wax model can lead to significant material waste.
Personalization Options
One of the appealing aspects of lost wax casting is the wide range of personalization options available. Each jewelry piece can be tailored to individual preferences, allowing for unique combinations of materials, designs, and finishes. This flexibility makes the technique especially popular among customers seeking distinctive items. For gemstone artwork, this personalization extends to the choice of stones, which can significantly alter both the look and value of a piece. However, while personalization adds artistic value, it may also lead to longer production times and increased costs, which are crucial considerations for both the artist and the client.
Sculptural Creations
Sculptural creations utilizing lost wax casting represent an exciting domain of this technique. Artists use this process to create unique three-dimensional pieces that can adorn galleries or private collections. The ability to capture fine details in a sculpture is enhanced through this method, allowing for more expressive and dynamic forms. Furthermore, sculptural work can blend various materials, including metals and gemstones, contributing to depth and visual interest. The decision to utilize gemstones within sculptures not only elevates aesthetic value but also integrates spiritual and cultural symbolism.
Functional Art Pieces
Lost wax casting also has a functional aspect. Artisans can create objects such as bowls, utensils, and decorative items that serve practical purposes while also showcasing artistic expression. These functional art pieces often incorporate gemstones in their design, elevating their status as objects of utility into realms of artistry. Functional art made using lost wax casting can carry significant cultural value, reflecting craftsmanship and design philosophy. However, the challenge lies in balancing functionality with artistic intent, as strict functional requirements might limit creative expression.
The applications of lost wax casting in gemstone art emphasize its versatility and richness as a medium, enabling artists to create both personalized jewelry and striking functional pieces.
Advantages of Lost Wax Casting
Lost wax casting is a technique celebrated for its distinct advantages, especially regarding the intricate demands of gemstone artwork. This method has gained acclaim in jewelry making and sculpture due to its ability to create highly detailed and personalized items. The benefits extend from technical precision to the creative flexibility it affords artists and designers.
Precision and Detail
One of the most compelling advantages of lost wax casting is its capacity for precision and detail. The process allows for the production of fine features in artwork that other methods often cannot replicate. Each wax model can capture minute details, which are preserved through the final casting.
For instance, jewelry pieces created via lost wax casting often exhibit intricate designs and complex textures. This level of detail is essential for gemstone enthusiasts and collectors who value unique features in their pieces. Fine jewelry from brands like Tiffany & Co. or Cartier often use similar techniques to ensure their products maintain exceptional standards of craftsmanship.
Moreover, because the wax can be sculpted by the artist directly, there are fewer limitations on the design process. High-definition results come from the fact that molds can be created that mirror the original wax model without losing integrity during casting.
Flexibility in Design
Flexibility in design is another key advantage of lost wax casting. Artists can experiment with varied styles and concepts using this casting technique. The method allows for adjustments to be made to the wax model before finalizing it for casting. If a designer seeks a specific shape or artistic flair, alterations can easily be executed in the wax.
Furthermore, lost wax casting supports a wide array of materials. Artists can utilize different metals in the process, including gold, silver, and bronze. Each material can yield distinct finishes and characteristics that enhance the overall appearance of the gemstone artwork. This adaptability meets the needs of jewelers who aim to create personalized expressions through their pieces.
Additionally, the possibility of creating limited edition items or one-of-a-kind works becomes feasible, as the mold can be used for a single cast or multiple casts, depending on the artist's vision. This flexibility can cater to a diverse market, attracting both collectors of original artworks and those who appreciate more affordable reproductions.
"The beauty of lost wax casting lies in its ability to convert creativity into tangible art with precision and flexibility."
With the lost wax casting method, artisans navigate the delicate balance between imaginative freedom and technical accuracy, resulting in distinctive and remarkable designs that appeal to a high-IQ audience interested in gemstone artistry.
Challenges in Lost Wax Casting
Lost wax casting, while revered for its precision and artistic potential, presents several challenges that artists and jewelers must navigate. Understanding these challenges is vital for mastering the craft and enhancing the quality of the finished product. Recognizing the obstacles not only helps in mitigating problems but also in pushing the boundaries of creativity and innovation in gemstone artwork.
Material Limitations
When engaging in lost wax casting, materials play a crucial role in determining the overall outcome of the final piece. For example, the type of wax used influences the ease of carving, the smoothness of the surface, and the detail capabilities. Soft wax may be easy to manipulate but can be less durable during mold making and casting.
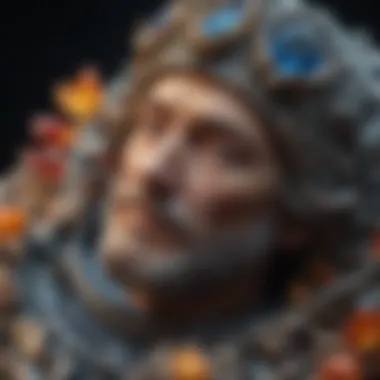
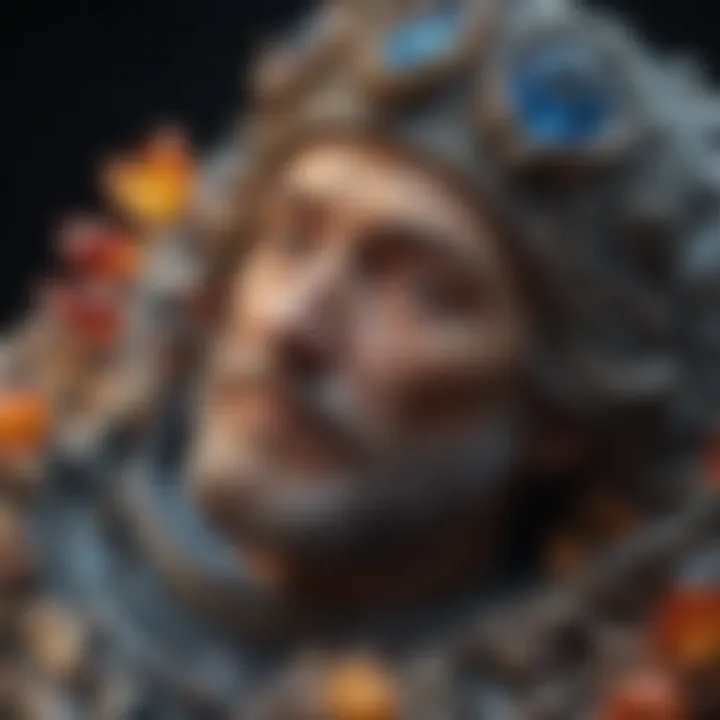
Conversely, hard wax provides durability but may present challenges in achieving finer details. Thus, selecting the right wax is key.
Furthermore, as the casting process progresses, limitations arise with the mold materials. Some molds are unable to withstand high temperatures required for different metals. This can lead to deformation or failure during the casting process. Artists often face a delicate balance of choosing materials that withstand heat while also allowing the intricate detail of the design to shine.
Lastly, the interaction between various gemstones and metals introduces its own set of complication. Some materials may react adversely, causing issues such as discoloration or even chemical reactions, affecting the integrity of the piece.
Technical Skill Requirements
Technical proficiency in lost wax casting is non-negotiable for successful outcomes. Mastering this craft requires a deep understanding of both the tools and techniques involved. Many artists start with basic skills but must progress to advanced techniques such as proper wax modeling and mold-making competencies.
A notable skill is the ability to design and create the wax model with precision. An improperly crafted model can lead to major flaws in the final cast. This modeling requires steady hands and keen attention to the details of the design. Even slight errors can result in significant imperfections during the casting process.
In addition, one must learn various methods for melting and pouring metals. Each metal has its own melting point and pouring characteristics. Understanding these properties is essential to avoid defects in the final product, such as air bubbles or incomplete fills. All of this contributes to the complexity and skill needed to master lost wax casting.
"The nuances of lost wax casting require not just artistry, but a solid grasp of material science and technical skills."
Moreover, time management and problem-solving skills are equally essential. Often, when setbacks occur, artists need to quickly analyze issues and adjust their methods.
Innovations in the Field
In the realm of lost wax casting, ongoing innovations play a crucial role in shaping the future of gemstone artwork. These advancements not only enhance the quality of the final products but also push the boundaries of creativity for artists and designers. Understanding these innovations is essential for anyone involved in gemstone art. They highlight the dynamic nature of this field, demonstrating how new techniques and materials can lead to improved efficiency, precision, and sustainability.
New Materials and Technologies
The landscape of lost wax casting has evolved significantly with the introduction of new materials and technologies. Traditional methods often relied on specific types of wax and metal alloys, but recent developments have introduced a range of alternatives that offer various benefits. For instance, some artisans are now utilizing specialized wax products that burn out more cleanly than conventional waxes. This reduces residue and simplifies the casting process, consequently increasing the purity of the final metal piece.
Technological advancements in 3D printing are also influential. By enabling artists to create highly intricate wax models directly from digital designs, this technology allows for greater experimentation and less material waste. 3D-printed wax models can capture complex details that would be difficult to achieve by hand. Moreover, the precision of these printed models leads to enhanced detail in the finished piece, appealing to those seeking uniqueness in their gemstone art.
Sustainability Practices
Sustainability has become a key concern in all fields, including lost wax casting. Artists and researchers are increasingly aware of their impact on the environment and are actively seeking ways to minimize their carbon footprint. One promising approach involves sourcing materials responsibly. Many gemstone artists are now opting for recycled metals and ethically sourced gemstones. This not only supports environmental sustainability but also aligns with consumer values.
Additionally, practices such as reducing waste during the model-making process have gained attention. By adopting techniques that utilize minimal wax or implementing better mold-making practices, artists can significantly decrease the amount of waste generated.
"Innovations in materials technology are reshaping the paradigm of lost wax casting, paving the way for a more sustainable and artistically vibrant future."
Furthermore, many gemstone artists are exploring green casting options, including the use of eco-friendly waxes and casting alternatives. These materials are designed to provide the same intricate results as traditional wax while being less damaging to the environment. As the focus on sustainability grows, these innovative practices may very well become industry standards, promoting a more responsible approach to gemstone craftsmanship.
Finale and Future Prospects
The exploration of lost wax casting molds holds significant value for gemstone artists and enthusiasts alike. This method is not only a traditional craft but also a foundation for innovation in the realm of gem art. The conclusion of this article emphasizes the multi-dimensional aspects of lost wax casting, underscoring its enduring relevance and future potential in gemstone creations.
One cannot overlook the benefits gleaned from mastering lost wax casting. The precision offered by this technique allows artisans to produce remarkably detailed and unique pieces, positively influencing the market for gemstone art. Further, new materials and technologies promise to enhance the capabilities of this method.
As practitioners navigate the challenges associated with the craft, they are also encouraged to embrace emerging trends. The shift towards sustainability practices, for instance, presents a unique opportunity to align gemstone artwork with environmental considerations. Artists are tasked with not only perfecting their craft but also integrating responsible sourcing and production methods.
"The combination of rich historical context and modern innovation makes lost wax casting a vital component of the future in gemstone artistry."
Summary of Key Points
- Precision and uniqueness: Lost wax casting allows for intricate designs, resulting in one-of-a-kind artworks.
- Innovation in materials: Ongoing research and development in mold-making materials are providing new avenues for artists.
- Sustainability focus: A growing emphasis on eco-friendly practices is shaping the future of gemstone casting.
- Skill development: As techniques evolve, so too does the demand for skilled artisans adept in both traditional and contemporary methods.
The Future of Lost Wax Casting in Gemstones
Looking forward, the future of lost wax casting in gemstones is both promising and dynamic. The integration of new technologies, such as 3D printing, is already influencing the traditional approach, allowing for greater customization and efficiency in the design process. Artists who adopt such innovations can expand their creative boundaries, catering to an increasingly diverse audience.
Additionally, collaborations between gemstone artists and tech developers may lead to new artistic forms and methods, redefining what can be achieved through lost wax casting. This represents a significant shift, as the melding of age-old traditions with modern technologies opens up possibilities that were previously unimaginable.
Sustainability will play a crucial role as well. Consumers are becoming more discerning, preferring to support artists who prioritize eco-conscious practices. By adopting sustainable materials and processes, artists not only meet this demand but also contribute positively to the environment.