In-Depth Analysis of Faceting Equipment for Gemstones
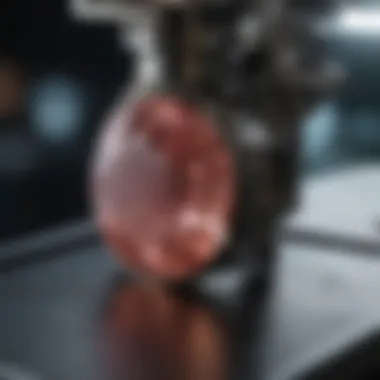
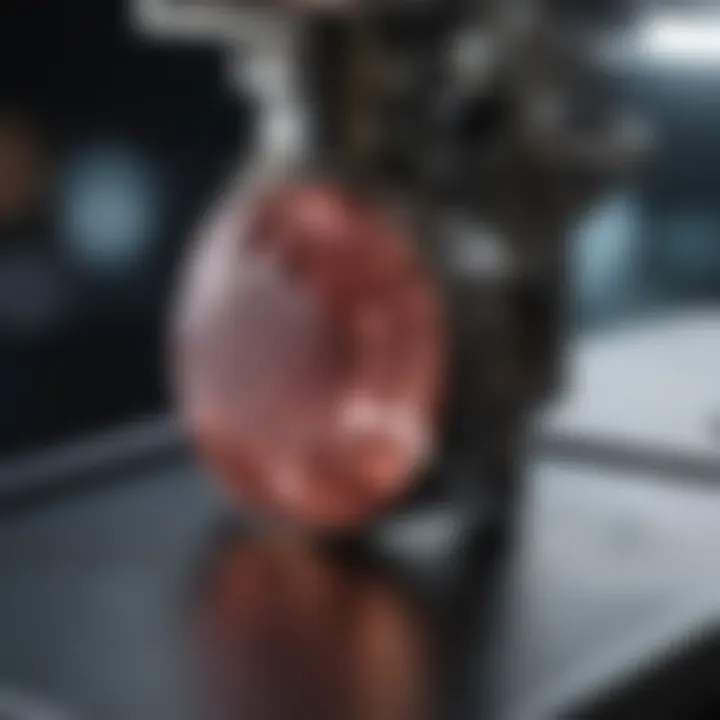
Intro
In the vibrant world of gems and jewelry, the process of transforming raw stones into breathtaking masterpieces hinges largely on the equipment used for faceting. Gemstone enthusiasts and professionals alike appreciate that the art of cutting is not just about shaping; it encompasses a deep understanding of instrumentation and technology at play. Faceting machines, precision techniques, and ongoing advancements play a pivotal role in enhancing both the aesthetic and monetary value of gemstones.
This article unpacks numerous aspects surrounding faceting equipment, guiding readers through the essentials of machinery types, the science of precision cutting, and maintenance practices that ensure longevity. This deep dive caters to a mixed audience— whether you are a collector searching for the perfect cut or a jeweler looking to refine your craft, this exploration promises enlightening insights into the world of faceting equipment.
Gemstone Overview
Description of the Gemstone
Before plunging into the intricacies of faceting machinery, it's helpful to paint a broad picture of what we mean when we speak of gemstones. These natural wonders are formed through a complex interplay of geological conditions, often involving thousands of years of crystallization. They come in various forms—diamonds, sapphires, rubies, and many more—each boasting unique charms and characteristics.
Physical Properties
Gemstones are defined by their physical properties, which include:
- Hardness: Measured on the Mohs scale, this determines a stone's resistance to scratching. For instance, diamonds rank highest at 10.
- Refractive Index: This property indicates how much light bends when entering a gem. It’s crucial in defining brilliance and sparkle.
- Specific Gravity: A measure of density, which helps in distinguishing between similar-looking stones.
These properties affect not just the appearance but also the cutting techniques used during the faceting process. Jewelers must understand these factors well to achieve optimal results, making the choice of faceting equipment all the more significant.
The Significance of Faceting Equipment
Faceting is a blend of art and science. The right equipment can transform a modest rough gemstone into a showcase piece. Each piece of equipment, from the cutting wheel to the polishing wheel, is designed for specific aspects of the faceting process. It’s like an orchestra, where each instrument plays its part meticulously to create a masterful symphony.
Types of Faceting Equipment
Understanding the various types of faceting machines is vital for any amateur or professional in this field:
- Manual Faceting Machines: Often preferred by seasoned jewelers, these allow for greater control and precision.
- Computerized Faceting Machines: Equipped with advanced technology, these machines automatically guide the cutting process, reducing human error.
- Polishing Machines: After cutting, polishing is key to achieving that coveted shine. These machines help enhance the brilliance of the stone.
"The right tool for the right job makes all the difference when crafting beauty from nature."
In our rapidly evolving technological landscape, modern advancements continue to reshape this craft, introducing innovative features that simplify and enhance the cutting process. This exploration will delve deeper into these subjects, examining how technology intertwines with tradition to carve out future possibilities in gemstone faceting.
Understanding Faceting Equipment
In the realm of gemstone cutting, faceting equipment holds a pivotal role. Its importance cannot be overstated as it lays the groundwork for transforming raw stones into finely crafted gems. Properly utilizing faceting machinery not only influences the quality of the final product but also impacts the efficiency of the entire cutting process. Understanding these tools helps jewelers and enthusiasts alike appreciate the level of precision involved in creating beautiful gemstones.
Definition of Faceting Equipment
Faceting equipment refers to a range of machines and tools specifically designed for shaping and polishing gemstones to enhance their aesthetic appeal and market value. At its core, this equipment includes various components that facilitate cutting, grinding, and polishing stones to achieve the desired facets. The machinery can be simple manual setups or sophisticated automated systems.
To define it succinctly, faceting equipment is the bridge between raw mineral and finished product, showcasing the artistry and craftsmanship of the jeweler. This definition extends beyond basic tools; it encompasses the complexities of technology woven into the art of faceting.
Role in Gemstone Cutting
Faceting equipment serves multiple key roles in the art of gemstone cutting, among them:
- Precision: The most apparent role is to enable precise cuts and angles, which are crucial for maximizing the stone's brilliance and light performance. The right machine settings lead to proper light refraction, enhancing the stone’s visual allure.
- Efficiency: Advanced faceting machinery can significantly reduce the time taken to craft a gemstone. Automated and hybrid systems allow for faster turnaround times without sacrificing quality.
- Versatility: The equipment is adaptable to different sizes and types of gemstones. Whether it’s a simple quartz or a complex diamond, the right faceting setup can accommodate varying hardness and cutting requirements.
- Quality Control: Modern machines are fitted with digital measurement tools that ensure consistent quality. This minimizes human error and ensures that the specifications meet industry standards.
This interplay of roles highlights the necessity of high-quality faceting equipment in achieving superior gemstone cutting results. By understanding the significance of these tools, gemstone enthusiasts and professionals can better appreciate the detailed craftsmanship that goes into each piece they admire.
Types of Faceting Equipment
Understanding the various types of faceting equipment is fundamental for anyone engaged in gemstone cutting. The equipment not only determines the quality and precision of the cut but also affects the efficiency and ease of the overall crafting process. Given the diverse nature of gemstones and the different styles of cuts, knowing the characteristics and advantages of each type of faceting machine is key. Whether you're a seasoned professional or a passionate hobbyist, selecting the right machine can make all the difference in your work.
Manual Faceting Machines
Manual faceting machines are often considered the traditional choice among gem cutters. These machines require the operator's skilled hands to oversee the cutting process. They tend to be more affordable than their automated counterparts, making them accessible for beginners and those who prefer a hands-on approach.
One notable feature of manual machines is the versatility they offer. Operators can adjust angles and settings with precision, allowing for a level of customization that automated machines may not provide. This can be particularly valuable when working with unique or irregularly shaped stones. Moreover, many experienced gem cutters appreciate the control that manual machines afford, as they can vary their technique based on the specific stone they are working on.
However, the trade-off is that using manual faceting machines demands a significant investment of time and effort. Learning to operate these devices effectively takes practice, and achieving consistent results can be challenging for novices.
Automated Faceting Machines
For those looking to streamline their gemstone cutting, automated faceting machines offer a modern solution. These machines are designed to minimize the manual effort involved in the cutting process, utilizing advanced technology to execute intricate designs with precision and speed.
One standout aspect of automated machines is their ability to replicate specific cuts with utmost accuracy. This consistency is particularly beneficial when working on larger batches of stones where uniformity is essential. Additionally, the time savings gained through automation can be significant, allowing professionals to take on more projects without compromising on quality.
However, there's a downside. Automated machines can be a considerable financial investment, limiting their accessibility for those on a tight budget. Furthermore, over-reliance on these machines might stifle the development of manual skills, as operators may not have as much overall experience handling various types of stones.
Hybrid Faceting Systems
Hybrid faceting systems combine the best features of both manual and automated machines. These systems allow for automated cutting processes while still providing the operator with the flexibility to make manual adjustments. For gem enthusiasts who find themselves in between traditional techniques and technology, hybrid systems can be an excellent choice.
The adaptivity of hybrid machines makes them suitable for a variety of settings—from professional workshops to smaller home setups. They can handle complex cuts with automated efficiency while still allowing for those nuances that a seasoned hand might bring to a stone.
In summary, each type of faceting equipment has its merits and drawbacks. The decision on which to use should hinge on one’s skill level, budget, and the specific requirements of their projects. Understanding these equipments is vital to producing stones that not only shine in beauty but also in craftsmanship.
"Understanding your tools not only enhances your skill but also elevates the quality of your work."
Remember, the right machine can elevate your gemstone cutting to impressive new heights.
Key Components of Faceting Equipment
When it comes to faceting equipment, understanding the key components is crucial for anyone serious about gemstone cutting. This equipment is not merely a collection of tools; each piece plays a significant role in assuring the quality and precision of your final product. In this section, we'll look into faceting heads, dop wax and dops, and grinding and polishing wheels, dissecting their functions and importance in the overall faceting process.
Faceting Heads
The faceting head is often considered the heart of any faceting machine. It’s the component that holds the gemstone in place while the cutting takes place. A precise faceting head will guarantee that the stone is held securely, allowing for effective and accurate cuts. This stability is vital, since even a slight wobble can lead to catastrophic results in the cutting process.
Moreover, many modern faceting heads come with adjustable features. This allows the user to alter the angle of the cut, accommodating various gemstone shapes and sizes. For example, with a well-designed faceting head, you can easily transition between cutting a delicate sapphire or a robust garnet, each requiring a different approach.
- Advantages of Well-Designed Faceting Heads:
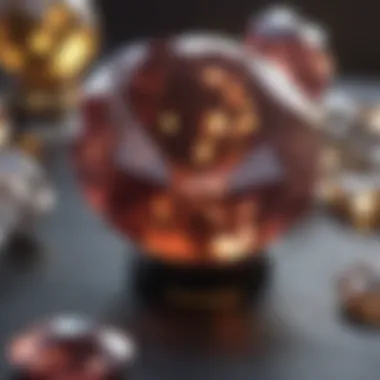
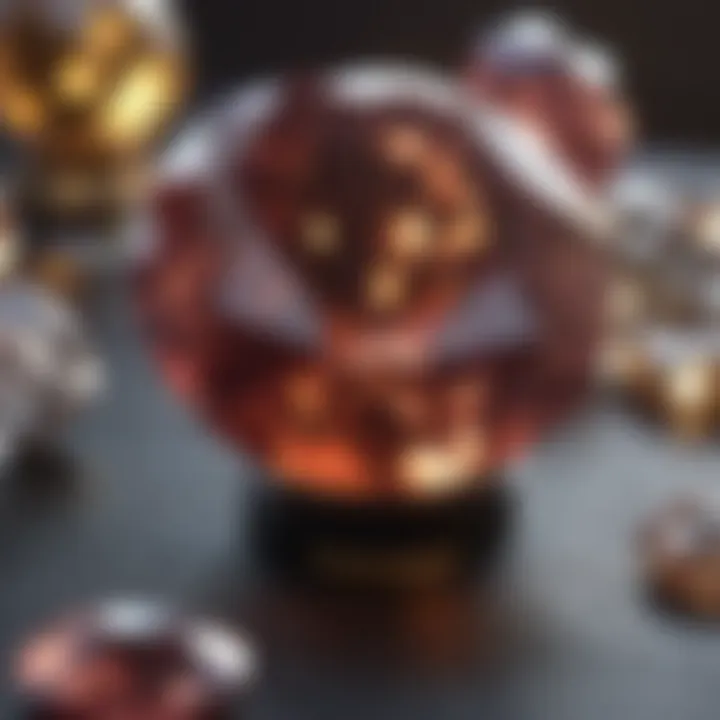
- Improved cutting precision
- Enhanced durability under consistent use
- Flexibility for various cutting styles
Dop Wax and Dops
Next up is dop wax and dops. This might sound trivial, but the combination of these two elements is essential for successful gemstone faceting. Dop wax is the adhesive used to attach the gemstone to its dop, a metal rod. This setup allows the cutter to manipulate the stone easily.
Using dop wax which has the right melting point is crucial. Too low, and the heat from the cutting wheels could cause the wax to melt, leading to a disaster. Too high, and it won’t stick well at all. Moreover, the choice of dops can also be significant. Dops come in various shapes and sizes, tailored for different stone types.
A few pointers when working with dop wax and dops:
- Always ensure the wax is at the proper temperature before use.
- Utilize the appropriate type of dop for the specific gemstone to avoid damaging it.
- Maintain your dops by cleaning off any residual wax or debris after use.
Grinding and Polishing Wheels
Lastly, we can't overlook the grinding and polishing wheels. These components are essential for shaping and finishing the gemstones. Grinding wheels are typically made from diamond or other abrasive materials that remove material efficiently while maintaining a level of control. They come in various grits, allowing for initial shaping all the way to the fine touches before polishing.
Polishing wheels, on the other hand, are designed to deliver that brilliant shine we all admire in gemstones. Using the right combination of grinding and polishing wheels can make or break the final appearance of your stone. Different wheels serve diverse functions: some are designed for shaping, while others excel at providing a smooth, reflective finish.
"Remember, the right wheel can turn a basic stone into a showstopper."
- Important aspects to consider for wheels:
- Choose the right grit according to the stage of cutting.
- Regularly inspect the wheels for wear and replace them as needed.
- Opt for high-quality wheels to ensure the best finish possible.
Selecting Faceting Equipment
Selecting the right faceting equipment is a cornerstone in the craft of gemstone cutting. It's not just about acquiring tools; it's about investing in the right technology to achieve precision, enhance creativity, and, ultimately, create pieces that captivate. Each piece of equipment plays a unique role in the faceting process and can significantly influence the outcome of your work.
Criteria for Choosing Equipment
When it comes to choosing faceting equipment, there are a several considerations to keep in mind that can help guide your decision:
- Skill Level: Beginners may benefit from user-friendly, manual faceting machines, allowing them to learn the craft at a comfortable pace. Experienced gem cutters might lean towards automated machines or hybrids for efficiency and complex designs.
- Desired Outcomes: If intricate designs with high precision are your goal, investing in sophisticated models with advanced features can make a difference. For simpler projects, a basic unit might suffic.
- Size and Space: Consider not just the size of the machine, but also the workspace required. A larger machine may offer more features but could also necessitate adjustments in your workshop layout.
- Durability and Build Quality: Look for equipment made from robust materials. Higher-quality machines may have a higher upfront cost, but they often save moeny in repairs or replacements down the line.
Budget Considerations
Your wallet can significantly dictate the type of faceting equipment you'll buy. While it's tempting to go for the newest tech on the block, cost-effectiveness can be just as critical:
- Initial Investment: Establish a budget before you start shopping. Settle on a range that you are comfortable with, leaving a cushion for unexpected expenses.
- Long-Term Value: Sometimes, a pricier machine may actually offer better long-term value because of its capabilities and durability. Considering lifespan and the potential to add more functions in the future might justify the splurge.
- Additional Costs: Don't forget to factor in accessories or replacement parts that might be necessary for your selected machine. Such as polishing wheels or specialized dops can add to your initial costs, so budget accordingly.
Brand Comparisons
Brand reputation can speak volumes when it comes to selecting faceting equipment. Each brand offers its own unique advantages, influencing your decision:
- Established vs. New Brands: Some well-established brands have a long history of reliability and support, which can be invaluable for newcomers. Meanwhile, newer brands might offer innovative features that attract seasoned cutters.
- Customer Reviews: Before making a purchase, check online reviews and community feedback on platforms like Reddit or specialized forums. This can give insights into real-world performance and user satisfaction.
- Warranty and Support: Ensure the brands you consider offer good warranties and customer support. This will be an important factor if you face issues down the road.
"Investing in the right faceting equipment isn't just a purchase; it's an investment in your craft that can elevate your work to new heights."
Taking the time to assess your needs, budget, and brand choices will lead to a more informed decision, ultimately aiding you in mastering the intricate art of gemstone faceting.
Operating Faceting Equipment
Operating faceting equipment is a foundational aspect of gem stone cutting. The mastery of such tools not only contributes to the precision in crafting breathtaking gems but also speaks volumes about the operator's expertise. Whether you are a newcomer looking to dip your toes into the world of gemstones or a seasoned professional fine-tuning your skills, understanding how to operate this equipment effectively is key to achieving desirable results. In this section, we will delve into the various procedures, techniques, and adjustments needed to optimize the performance of faceting machines.
Initial Setup Procedures
Setting up faceting equipment is akin to assembling a finely-tuned orchestra. Each piece plays a vital part in ensuring that the final output is harmonious.
- Choosing the Location: Start by selecting a stable workbench that is well-lit to prevent any errors that could stem from poor visibility.
- Installing the Faceting Machine: Ensure that the machine is level; an even setup helps maintain accuracy during the cutting process.
- Mounting the Gemstone: Use the dop stick along with dop wax to securely attach the gemstone. A firm hold is necessary to avoid any slips during cutting.
- Setting Up the Faceting Head: Position the faceting head in a way that it aligns properly with the gemstone for optimal cutting.
Getting these steps right can save you from countless headaches down the line, as any misalignment can lead to sub-par finishes.
Common Techniques for Faceting
Faceting isn't just about having the right equipment; it's also about the techniques employed. Mastery of these techniques can significantly enhance the aesthetics and scintillation of the gemstones. Some common techniques include:
- Bruting: This is the initial shaping process where the stone is roughly shaped into a round form, often compared to sculpting a block of marble.
- Faceting: The actual cutting of facets involves specific angles. Understanding the interplay of light with each facet can drastically affect the stone's brilliance.
- Polishing: After faceting, the stone undergoes polishing to achieve the desired finish. It’s akin to putting the final touches on a masterpiece.
Learning these techniques can feel overwhelming at first; however, with practice, the steps soon become second nature.
Adjusting Settings for Precision
Achieving precision in gemstone cutting is somewhat of an art form and requires familiarity with the machine's settings. Here are a few considerations:
- Angle Measurement: Using a digital protractor can help in adjusting angles with precision, ensuring that each facet is cut to the desired alignment.
- Speed Control: Adjusting the speed of the grind is essential. Too fast can lead to mistakes; too slow might waste unnecessary time.
- Depth Control: It's important to monitor the depth as you progress. Frequent checks will allow for finer adjustments and ensure that the facets are even and aligned.
Tip: Regular practice and a keen eye will sharpen your ability to adjust these settings accurately, leading to cleaner cuts and better quality stones.
In sum, operating faceting equipment is as much about the machinery as it is about the operator's touch and skill. The combination of proper procedures, techniques, and precision adjustments can turn average stones into sparkling gems that catch the eye. Understanding each component can elevate the level of craftsmanship and ultimately enhance the beauty and value of the finished product.
Maintenance of Faceting Equipment
Maintaining faceting equipment is crucial for anyone invested in the art of gemstone cutting. The precision required for crafting gemstones is not just a result of skill; it also heavily relies on the consistent performance of the tools used. Keeping these machines in optimal condition reduces the likelihood of errors and enhances the quality of the final product. Regular maintenance ensures that the equipment can deliver high performance, leading to better efficiency and workflow. When a machine operates well, it not only results in fewer mistakes but also saves time and resources, providing a significant benefit for both hobbyists and professionals alike.
Cleaning Procedures
Cleaning is the first and foremost step in equipment maintenance. Over time, residue from grinding and polishing can build up and negatively affect performance. Neglecting to clean the equipment can lead to dull tools, poor surface finishes, and inconsistent results. Here are a few effective cleaning steps:
- Regularly wipe the surfaces of the faceting machine with a soft, damp cloth.
- Use a brush or compressed air to remove fine dust and debris from hard-to-reach areas.
- For stubborn residue, a mild detergent can be mixed with water, but ensure to dry everything thoroughly after cleaning.
A well-maintained machine not only performs optimally but also extends its lifespan. Keeping these machines clean can feel like a small task but it packs a powerful punch.
Regular Maintenance Practices
Just like a car needs oil changes, faceting equipment has its own list of regular maintenance requirements.
- Lubrication: Make it a habit to apply lubricant to moving parts according to the manufacturer’s instructions. Proper lubrication reduces friction and wear over time.
- Alignment Checks: Often overlooked, alignment can impact the angles and facets being created. Regularly check and adjust the faceting head to ensure precision.
- Calibration: Periodically check the calibration of the machines. This guarantees that all measurements are accurate and consistent across projects.
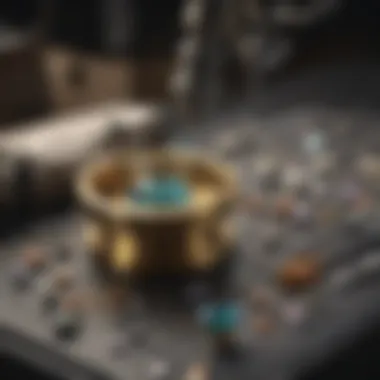
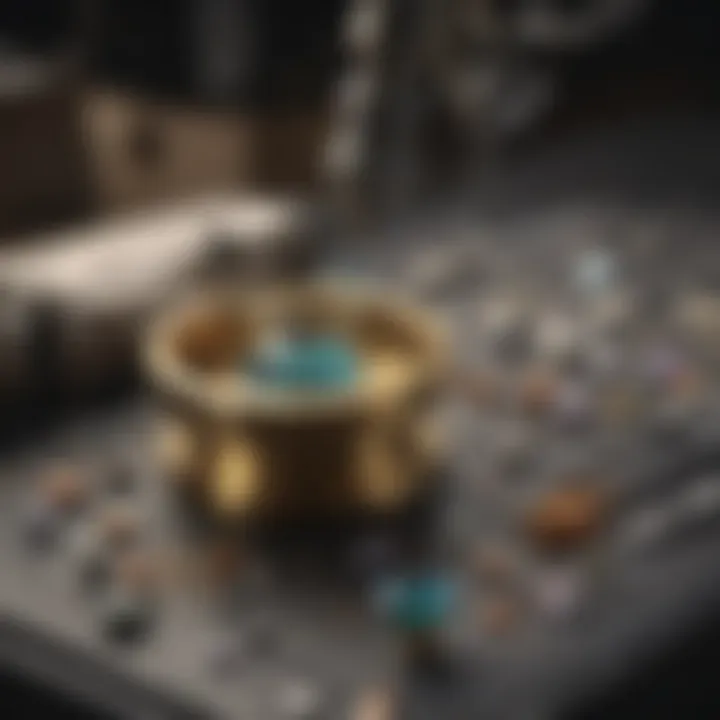
Establishing a maintenance schedule is beneficial. It becomes routine and ensures that nothing is overlooked over time. Consider jotting down a checklist or keeping a log of maintenance tasks completed.
Replacing Worn Parts
Eventually, wear and tear are inevitable. Knowing when and how to replace parts is vital for the long-term success of your faceting efforts. Signs that parts may need replacing include:
- Unusual noises during operation.
- Decreased precision or performance.
- Visible fraying or deterioration of components.
When replacing worn parts, it’s essential to use the correct specifications. Sourcing replacement parts from reputable vendors can make a significant difference in maintaining the equipment’s performance.
For instance:
- Motors should be replaced with models that match the original specs to avoid functional mismatches.
- Polishing wheels should be changed regularly to ensure optimal polishing performance.
Ultimately, replacing worn parts when necessary is crucial to ensure the machinery runs smoothly and effectively. It avoids costly mistakes in the long run.
In summary, a well-maintained faceting machine is a key to impeccable gemstone cutting. Neglecting maintenance can lead to disastrous outcomes.
By keeping a close eye on cleaning, regular upkeep, and timely replacements, you secure not just the tools themselves, but also your craft.
Technological Advancements in Faceting
In the realm of gemstone cutting, technological advancements in faceting play a pivotal role in transforming the art into a precise science. The influence of modern technology is felt not just in the efficiency of the processes, but also in the quality of the finished stones. From the shift toward automation to the integration of sophisticated design software, these innovations are reshaping practices that have stood the test of time.
One key aspect is the introduction of computer-aided design (CAD) tools, which allow artisans to create intricate designs with unrivaled precision. This modern method enables the visualization of the gemstone's final form as a digital model before it is ever cut into stone, drastically reducing the chances of mistakes. Instant feedback and simulation capabilities within CAD platforms ensure that the designs maximize the gem’s potential, enhancing light performance and overall aesthetics.
Computer-Aided Design in Faceting
The intersection of computer technology and gemstone faceting has resulted in a revolutionary approach to jewelry making. Computer-aided design in faceting offers a predictable workflow that can significantly improve productivity for both hobbyists and professionals.
- Precision: CAD allows for minute calculations regarding angles and facets, producing more consistent and symmetrical results compared to manual methods. This precision plays a crucial role in how light interacts with the stone, directly impacting its brilliance.
- Customization: Aspiring jewelers can experiment with styles without committing to hard materials until they find the perfect design. The ability to create and edit designs easily opens the door to personalization that was previously limited.
- Visualization: Seeing a 3D model gives designers the opportunity to understand complex designs better and make necessary adjustments before cutting. This feature can save not just materials but also time.
In this fast-paced industry, operating with precision and flexibility is non-negotiable.
Innovations in Grinding Techniques
Grinding techniques have also seen notable innovations, with advancements aimed at improving both effectiveness and safety. Historically, faceting was labor-intensive and time-consuming, requiring artisans to rely heavily on skill and experience. Now, modern machines incorporate options like variable speed motors and coolant systems that enhance the grinding process.
- Speed and Efficiency: These modern machines can finish the faceting process in a fraction of the time it used to take. This speed allows more gemstones to be processed without compromising quality.
- Quality Control: New grinding wheels designed with various materials allow for finer control over the grinding process. Innovations such as diamond-coated wheels offer smoother finishes and better overall results, making rough stones easier to tackle.
- Safety Features: Contemporary equipment often comes with improved safety features, reducing the risk of accidents in what can be a hazardous environment with sharp cutting tools and dust.
These innovations help keep the craft alive while making it more accessible to newcomers in the industry.
Impact of Digital Measurement Tools
Digital measurement tools have become indispensable in the realm of faceting, streamlining quality assurance processes and enhancing the accuracy of measurements. By utilizing high-precision instruments, gem cutters can achieve previously unattainable levels of detail in their work.
- Laser Measurement: Tools that utilize laser technology can measure angles and dimensions at an unparalleled resolution. This allows for fine-tuning adjustments that directly apply to cutting strategies.
- 3D Scanners: The use of 3D scanning provides a way to quickly assess the geometry of the stone before and after faceting. This comparison might uncover imperfections unnoticed by the naked eye.
- Archival Data: These digital tools also enable the documentation of measurements. This records not just the specifics of one gemstone but contributes to a knowledge base for future projects.
The blend of these digital tools with traditional craftsmanship forms the backbone of modern gemstone faceting, cultivating an environment ripe with potential and advancement.
"The future is not something we enter. The future is something we create." – Leonard I. Sweet
In summary, technological advancements are revolutionizing the art of faceting. They enable better designs, faster production, and higher-quality gemstones, enhancing the craft for both seasoned professionals and newcomers alike.
The Art of Faceting
The art of faceting goes beyond mere mechanical processes; it’s a harmonious blend of science, skill, and creativity. For gemstone enthusiasts and collectors, the quality of a gemstone largely hinges on how it is cut and shaped. Proper faceting not only boosts a gemstone's beauty but also its value and marketability. When done right, faceting can transform a rough stone into a dazzling piece that catches the eye and dances with light. Understanding the nuances of this craft helps jewelers and designers make more informed decisions while enhancing their own artistic expressions.
Design Principles in Faceting
At the heart of every remarkable faceted gemstone lies solid design principles. Design, in terms of faceting, refers to the arrangement and geometry of the facets, which are the flat surfaces of a gemstone. A well-designed stone balances various factors:
- Proportion: Proper proportions ensure that light enters and exits the stone efficiently, influencing brilliance and fire.
- Symmetry: Symmetrical designs provide an aesthetic appeal that can elevate a stone's value significantly.
- Facet Arrangement: The specific placement and angles of the facets can either enhance or diminish light performance.
When a gemcutter considers these elements, they don't just follow a set template; they adapt to the unique characteristics of each gemstone. Custom designs account for the inherent qualities of the raw material, making each finished piece a true one-of-a-kind creation.
Understanding Gemstone Symmetry
Gemstone symmetry is a critical element that gem cutters must grasp. It refers to the uniformity in shape and distribution of the facets around a stone. It might seem like a small detail, but uneven symmetry can lead to uneven light distribution, which affects how sparkly and lively a stone appears. Here are some key points about gemstone symmetry:
- Balance: Symmetry ensures that light is reflected evenly across the gemstone, enhancing its visual appeal.
- Market Value: Well-symmetrical stones often demand higher prices due to their perceived quality.
- Design Consistency: It helps maintain a coherent design throughout the piece, which can be paramount in high-end jewelry creation.
Thus, understanding and executing the principles of symmetry become essential skills for any professional in the field. Even small deviations can spoil the desired outcomes.
Visualizing Light Refraction
Light refraction is what can make or break a faceted stone, and understanding this principle can significantly improve the quality of faceting. When light strikes a gemstone, it bends and splits into various colors; this phenomenon is known as dispersion. A good cut maximizes thislight play, resulting in gems that sparkle and attract attention. Here’s how faceters can visualize and manipulate light refraction:
- Angle Consideration: The angles at which facets are cut directly influence how light enters and exits.
- Critical Angles: Faceters need to calculate the critical angles for each type of gemstone to optimize brilliance and minimize light loss.
- Polishing Techniques: Proper polishing enhances surface quality, allowing for smooth light passage through the stone.
"A well-cut gemstone is not just about achieving the right shape; it’s about orchestrating light in such a way that it creates an aesthetic masterpiece."
By grasping these principles of light behavior, gem cutters can elevate their craft, resulting in breathtaking results that appeal to both collectors and casual admirers alike.
Challenges in Faceting
Faceting, while an art form, presents numerous challenges that can frustrate even the most ambitious gemstone enthusiasts. Understanding these hurdles is crucial, not just for achieving desired aesthetics but also for ensuring that the valuable stones maintain their integrity throughout the cutting process. From technical difficulties to material quirks, grappling with these challenges can mean the difference between an exquisite piece of jewelry and an unfortunate mishap.
Common Errors and Their Solutions
Even seasoned gem cutters encounter pitfalls during the faceting process. Some of the more common errors include miscalculating angles and failing to secure the stone correctly.
- Angle Miscalculations: Getting the angles wrong can drastically affect how light interacts with the gemstone. To avoid this, one must invest time in measuring precisely and double-checking settings on the machine. Utilizing tools like protractors or digital angle finders can help ensure accuracy.
- Improper Securing of the Stone: If the gemstone is not securely fastened, it may shift during cutting, leading to uneven facets and wasted materials. A good practice is to use dop wax at the correct temperature to achieve optimal adhesion. If the stone does slide, returning to the initial setup and ensuring it’s properly mounted is critical.
"Attention to detail in angle calculation can save an artist from extensive reworking and materials loss."
Addressing Material Limitations
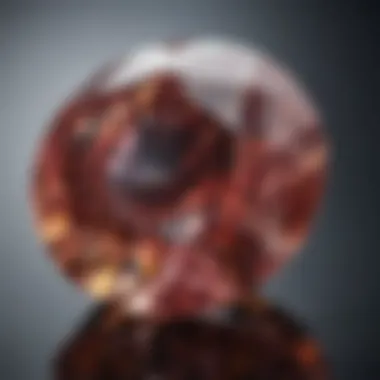
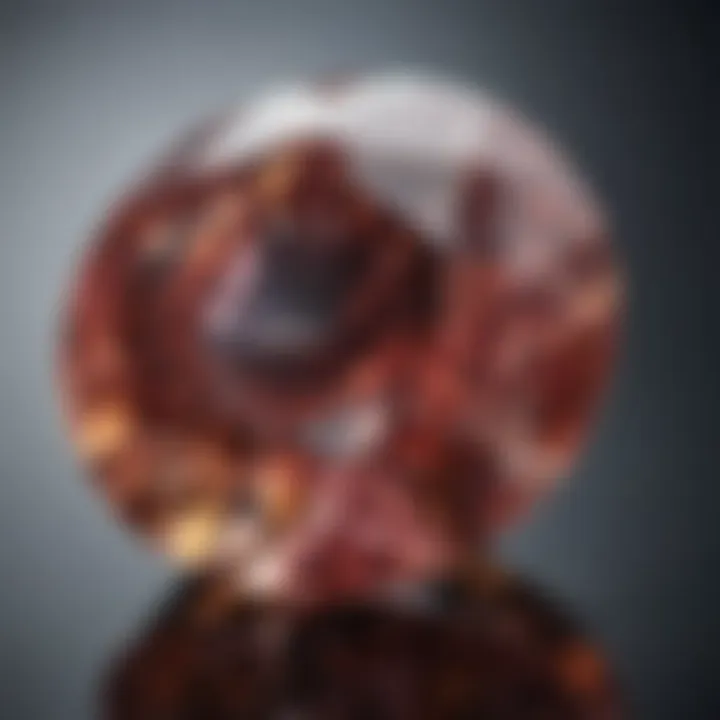
Not all gemstones are created equal, and some present unique challenges during faceting. Harder stones like diamonds require different approaches than softer types such as opals or emeralds.
- Hardness Variability: Each gemstone's hardness (measured on the Mohs scale) impacts how it should be cut and polished. Cutters need to identify the material characteristics beforehand. The use of the wrong tools can lead to chipping or scratches. Learning to pick appropriate wheels and drills is essential to safeguarding the material during the process.
- Inclusions and Flaws: Internal problems within the stone can lead to unexpected issues. Regularly examining the rough gemstone and understanding its internal structure aids in making informed cutting decisions. If a stone has numerous inclusions, creating smaller facets might mitigate the likelihood of breakage.
Dealing with Software Issues
With the increasing reliance on technology in gemstone faceting, software problems can be particularly concerning.
- Software Glitches: Automated faceting machines often come with software to help manage angles and designs. These systems can be temperamental at times. It's wise to have a backup plan, including manual techniques for critical situations. Regular updates of the software can also help in minimizing glitches.
- Training Needed for New Software: As new tools and software emerge in the industry, training becomes paramount. Not everyone finds adapting to new technologies easy. Investing in proper training sessions can significantly smoothen the transition and help in avoiding common operational errors.
In summary, facing the challenges of faceting equipment requires a mix of patience, skill, and knowledge. Being aware of potential errors, material traits, and technological challenges can help ensure a smoother cutting experience, leading to beautiful crafted gemstones.
Sustainability in Faceting Practices
When it comes to the delicate craft of faceting gemstones, sustainability has emerged as a significant concern. This facet, so to speak, of the gemstone industry focuses on reducing environmental impacts while upholding quality and craftsmanship in gemstone cutting. With more consumers becoming mindful of their choices, the call for eco-friendly practices in faceting is louder than ever. Here, we will unravel the various dimensions that highlight the importance of sustainability in faceting practices.
One glaring reason sustainability matters is the ever-growing concern about climate change and resource depletion. The gemstone industry, like many others, stands to be scrutinized for its environmental footprint. By embracing sustainable methods, artisans can not only contribute to a healthier planet but also attract a demographic that values eco-conscious decisions.
Benefits of Sustainability
Adopting sustainable practices in faceting offers a multitude of benefits:
- Reduced Environmental Impact: By using eco-friendly materials and techniques, workers can lessen the waste and pollution associated with traditional methods.
- Attracting a Conscious Consumer Base: As awareness rises, customers prefer buying gemstones cut through sustainable processes, enhancing their market appeal.
- Long-term Cost Efficiency: While some may view eco-friendly materials as costly upfront, many can save money in the long run due to less waste and improved efficiency.
Considerations
Even with the clear benefits, transitioning to more sustainable practices doesn't come without hurdles. For instance, the availability of eco-friendly materials can be limited, or there might not be enough information shared on the effectiveness of these alternatives. Moreover, some traditional craftsmen might be hesitant to change long-established techniques for fear of compromising quality.
Overall, while sustainability in faceting is an evolving topic, it already shows potential to reshape the industry positively.
Eco-Friendly Materials and Techniques
Incorporating eco-friendly materials and techniques into faceting practices is essential for reducing environmental impacts. This involves the adoption of materials that are not just safe for the environment but also ensure that gemstones maintain their natural beauty.
For instance, opting for synthetic dop wax can dramatically cut down on petroleum-based products that are often used in traditional methods. Additionally, many facetors are now turning to biodegradable lubricants during the cutting process, ensuring that chemical runoff is minimized.
It's worth noting that some artisans have even begun using recycled metals in their tools — a practice that, while might sound novel, goes a long way in conserving resources.
"Every gemstone deserves to shine, but that shine shouldn’t come at the cost of our planet."
Reducing Waste in the Faceting Process
Waste reduction is a crucial component when discussing sustainability in faceting. The gemstone industry has, in essence, been a waste generator, from offcuts during the cutting process to discarded outdated equipment.
Here are a few strategies that can help reduce waste significantly:
- Efficient Cutting Techniques: By utilizing advanced cutting techniques that maximize the yield from rough stones, faceters can diminish the amount of discarded materials.
- Reuse of Cuttings: Some craftsmen are creatively finding ways to utilize offcuts, turning them into smaller, unique pieces or jewelry components.
- Tool Maintenance: Regular maintenance of faceting tools ensures they remain effective longer, reducing the need for replacements.
Embracing these approaches can pave the way for a more sustainable future in gemstone faceting.
Ethical Sourcing of Gemstones
The conversation around sustainability doesn’t just stop at the tools and techniques — it also extends to where gemstones originate. Ethical sourcing of gemstones is becoming increasingly vital as consumers seek peace of mind that their stones are mined and acquired responsibly.
This means ensuring gemstones are sourced from mines where workers are treated fairly, and environmental practices are honored. Beyond just contributing to social justice, ethically sourced gemstones often come with certifications that assure the consumer of their integrity.
Also, as buyers become knowledgeable about the sources of their gemstones, they will likely reward brands that are transparent about their sourcing practices. This growing trend could lead to a significant shift in how gemstones are mined, paving paths toward more ethical operations.
In summary, sustainability in faceting practices is a multi-faceted issue that encompasses the adoption of eco-friendly materials, waste reduction strategies, and ethical sourcing of gemstones. As the industry evolves, those who embrace these concepts are likely to find themselves ahead of the curve, appealing to a demographic that values both quality and ethics.
Future Trends in Faceting Equipment
The landscape of faceting equipment is continuously evolving, driven by advancements in technology and changing consumer expectations. Understanding these trends is crucial for gemstone enthusiasts and professionals alike, as it allows them to stay ahead of the curve in an increasingly competitive market. Innovations not only enhance the efficiency of gemstone cutting but also improve the precision and quality of the final products. This insight is essential for anyone who aims to perfect their craft or invest wisely in faceting machinery.
Emerging Technologies and Innovations
Emerging technologies are reshaping the faceting equipment arena, making processes more streamlined and effective than ever. For instance, computer simulation software has garnered attention, providing gem cutters with the ability to visualize complex designs and outcomes before cutting begins. This approach saves time and minimizes material waste.
Moreover, advancements in machine learning and artificial intelligence are being incorporated into faceting machinery. These technologies allow machines to learn from previous cuts, optimizing settings in real-time based on user input and historical data. This leap in technology empowers users to produce precision cuts that enhance the beauty of gemstones, leading to better quality in the end product.
Market Predictions and Consumer Expectations
As technology evolves, so do market predictions. The gemstone industry is increasingly leaning towards customized solutions that cater to individual preferences. Consumers are no longer satisfied with generic cuts; they expect unique shapes and styles that reflect their personalities. This expectation drives demand for equipment that can handle intricate and specialized cuts.
Furthermore, from a market standpoint, experts predict a rise in eco-conscious consumerism. More buyers are looking at how gemstones are cut and processed, including the sustainability of practiced techniques and the materials used. This awareness encourages manufacturers to develop environmentally friendly faceting equipment. Responsive retailers will align their offerings to meet these emerging consumer preferences, thus securing their positions in a rapidly changing market environment.
The Role of Automation in Gem Processing
Automation holds a pivotal role in the future of gem processing. As automated faceting machines become more prevalent, they promise increased efficiency, safety, and output quality. These devices can handle repetitive tasks that otherwise may lead to fatigue for human operators, allowing skilled artisans to focus on more nuanced aspects of gemstone design.
Implementing automation also allows for greater precision in cuts. Automated systems are equipped with advanced sensors and computational techniques to ensure that each facet aligns perfectly with the next, leading to stunning finished pieces. Additionally, integrating automation reduces the chance for human error, a common pitfall in manual cutting.
"Automation isn't just a technological advance; it’s a critical shift towards achieving higher quality in every gemstone cut."
Epilogue
The intricate dance of faceting—where machines meet artistry—is pivotal in the world of gemstone cutting. In this article, we've mapped out the criss-crossing paths of technology and artistry in faceting equipment. These tools are not merely machines; they are the keys to unlocking the hidden brilliance of gemstones that dazzle the eye and captivate hearts. The very act of faceting transforms raw stones into sparkling treasures, making the understanding and choice of the right equipment absolutely essential for both enthusiasts and professionals.
Summarizing the Importance of Faceting Equipment
Faceting equipment lays the foundation for creating beautiful, high-quality gemstones. It’s not just the cutting that matters, but how precision is achieved through the right tools. Consider the various components, from faceting heads to polishing wheels, each plays a crucial role in ensuring a smooth transformation.
- Well-chosen equipment can lead to:
- Enhanced accuracy in cuts
- Improved gemstone luster
- Increased market value of finished products
By understanding these tools, users can harness the full potential of gemstones, making informed choices for both aesthetic appeal and profitability. The right equipment symbolizes a significant investment in craftsmanship, ultimately reflecting one’s skills and knowledge in the trade.
Encouraging Best Practices in Faceting
To ensure superior results in gemstone faceting, adopting best practices is key. Here are some essential approaches for enthusiasts and professionals alike:
- Regular Maintenance: Routine care of equipment, including cleaning and adjustments, fosters longevity.
- Proper Techniques: Gaining proficiency in techniques minimizes errors and maximizes efficiencies during the cutting process.
- Continuous Learning: Stay updated with advancements in technology and best practices in the industry, as these can profoundly affect outcomes.
- Eco-Friendly Choices: Consider sustainable practices by selecting eco-friendly materials, contributing positively to both the craft and the environment.
"Tools can only take you so far, but knowledge and practice will guide you toward excellence."
Proper education about the equipment and continuous practice leads to a level of mastery that not only benefits individual craftsmen but enriches the entire gemstone community. In closing, the importance of faceting equipment intertwines with best practices, ensuring that the art of gemstone cutting remains alive and vibrant in a continually advancing world.