Mastering Jewellery Wax in Gemstone Crafting
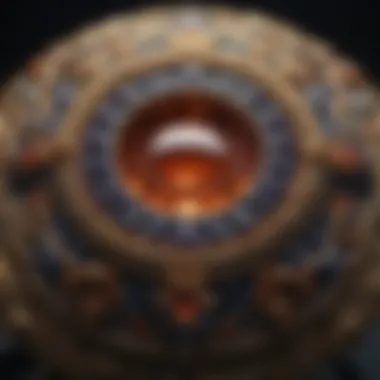
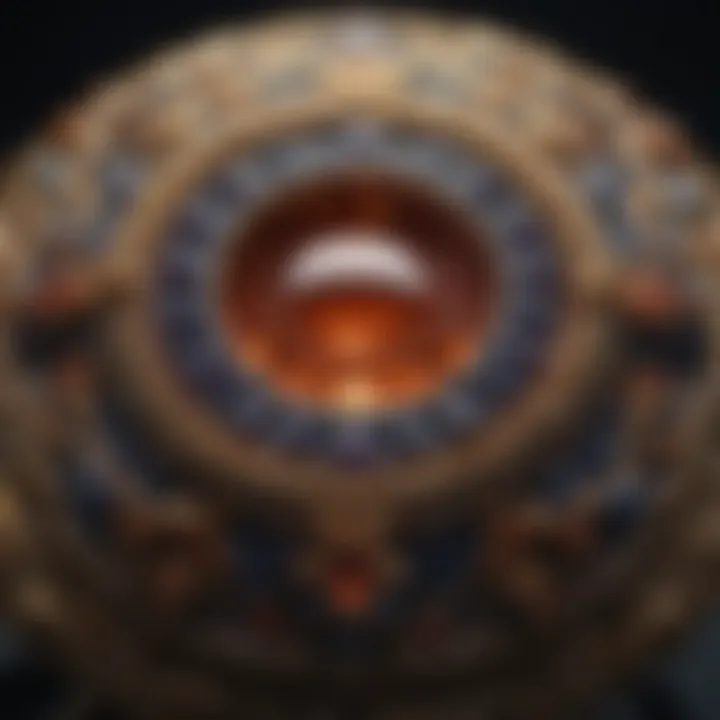
Intro
Jewellery making is not just an art; it's a symphony of creativity, precision, and tradition. At the heart of this intricate craft lies a material that often slips under the radar yet plays a pivotal role in gemstone artistry—jewellery wax. This article sheds light on the essential function wax serves in the craftsmanship of gemstone jewellery, navigating through the types of wax, techniques used in carving, and the tools that bring these creations to life. More than just a material, jewellery wax embodies the spirit of innovation and sustainability, making it a significant topic for both seasoned artisans and budding jewellery enthusiasts alike.
Let's embark on a journey through the fascinating realms of jewellery wax, unveiling the layers that contribute to its vital place in the gemstone crafting world.
Prelude to Jewellery Wax
Jewellery wax plays a crucial role in the realm of gemstone crafting, serving as a foundational element in the design and creation of intricate pieces. Understanding its significance can illuminate various aspects of jewellery-making that may otherwise seem mundane. It’s not just a material; it’s a dynamic tool that allows artisans and designers to breathe life into their visions.
The definition and purpose of jewellery wax extend beyond mere usability. Wax has the adaptability to be molded into virtually any shape, making it indispensable in the initial stages of crafting. As such, it provides a level of precision and flexibility that is often hard to come by with traditional materials. The tactile nature of wax, combined with its workability, enables jewellers to experiment and iterate designs without making a hefty commitment financially or materially.
Furthermore, the history of wax in jewellery making reveals a fascinating journey. It highlights how artisans over centuries have relied on this material to express their artistry. From ancient civilisations that used natural beeswax for casting methods to the contemporary formulations we see today, understanding its evolution also reflects the progression of the craft itself.
By examining these elements, we can appreciate not just the practical implications of jewellery wax, but also its emotional and cultural significance in the world of gemstones. The artistry of jewellery making is intricate and layered, and wax is one of its essential threads, making it a topic worthy of detailed exploration.
Types of Jewellery Wax
Understanding the types of jewellery wax is pivotal in gemstone crafting. Each type of wax serves unique purposes and presents distinct characteristics, making them suitable for various techniques and designs in jewellery making. This section will delve into three primary categories of wax used by artisans, highlighting their benefits and practical applications.
Paraffin-Based Waxes
Paraffin-based waxes are among the most commonly used materials in jewellery crafting. Their popularity stems from affordability and availability, making them an accessible option for both amateur and professional jewellers. These waxes are derived from petroleum, providing a stable, consistent medium that melts easily and can be molded into fine details.
The primary advantage of paraffin wax is its melting point, which is relatively low compared to other types of wax. This feature allows for rapid shaping, making it an ideal choice for intricate designs. However, one must be careful, as prolonged heating may degrade the wax.
Additionally, paraffin waxes can be blended with additives to enhance specific properties, such as flexibility and finish. Buying this wax in different hardness levels can extend its usage across various projects. In the world of gem crafting, this flexibility is crucial, allowing designers to achieve varying textures and precise contours.
Carnauba Wax
Carnauba wax is a natural wax harvested from the leaves of the Brazilian palm tree, known for its remarkable hardness and glossy finish. This type of wax holds a special place in high-end jewellery making, often used as a protective coating on finished pieces or in the creation of moulds due to its durability.
One significant aspect of carnauba wax is its higher melting point compared to paraffin wax. This characteristic can be both a benefit and a challenge. On one hand, it allows for a shinier finish, but on the other hand, it requires jewellers to work more carefully with temperatures when sculpting.
Many artisans commend carnauba wax for its eco-friendly nature, as it is biodegradable and derived from renewable sources, appealing to the environmentally conscious creator. Because of its unique properties, it can also act as a great base wax when mixed with softer waxes to improve surface quality and user experience throughout the carving process.
Specialty Waxes for Detailed Crafting
Specialty waxes cater to specific needs in the jewellery-making industry, offering enhanced characteristics that regular waxes might not provide. These waxes can range from composite materials containing synthetic components to natural blends featuring multiple wax types. The options are as diverse as the designs they aim to create.
Some of the benefits of specialty waxes include:
- Detail Precision: These waxes are tailored for fine, intricate designs, allowing artisans to carve out even the smallest details without compromising strength or integrity.
- Custom Formulations: Many suppliers offer waxes formulated for unique techniques, whether that be for casting processes, soldering, or even creating detailed textures that replicate organic forms.
- Varied Hardness: Depending on the project, artisans can choose from softer waxes for easy manipulation or harder ones for more stable structural integrity.
Using specialty wax can significantly enhance the quality of designs, enabling jewellers to push creative boundaries and achieve their desired aesthetics. A thoughtful approach to selecting the right type of wax can lead to magnificent outcomes in the final pieces, resonating with the artistry behind gem crafting.
Properties of Wax Used in Jewellery
When diving into the realm of jewellery wax, understanding its properties is like peeling an onion; there’s so much more beneath the surface. The attributes of wax not only define its functionality but also play a pivotal role in the crafting of intricate designs that characterize high-quality gemstone jewellery. In this section, we’ll explore key elements such as melting points, durability, flexibility, surface finish, and texture. Each factor contributes significantly to the overall effectiveness of wax in creating stunning jewellery pieces.
Melting Points and Workability
The melting point of a wax directly correlates to its adaptability during the crafting process. In jewellery making, achieving the right temperature is crucial. A wax with a lower melting point, like paraffin-based wax, becomes fluid and easy to manipulate when heated, allowing jewellers to carve and mold with exceptional ease. Conversely, higher melting point waxes can withstand more rigorous shaping without deformation.
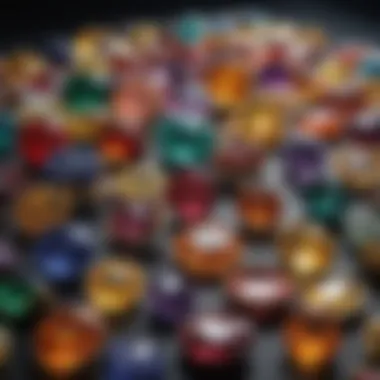
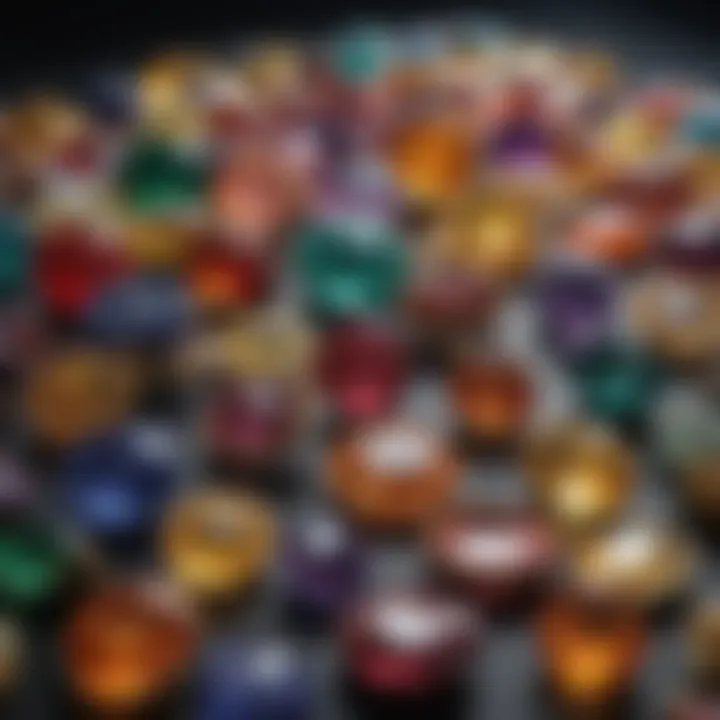
A clear understanding of melting points ensures that artisans can select the appropriate wax type for their specific needs. For instance:
- Paraffin-based waxes melt between 120°F to 160°F (about 49°C to 71°C), making them excellent for details and delicate pieces.
- Carnauba wax, known for its rigidity, has a much higher melting range, usually around 180°F to 190°F (82°C to 88°C), which is more suited for sturdy models.
The ability to control melting points also allows for precise craftsmanship, ensuring that details remain sharp and visually appealing during the cooling process.
Durability and Flexibility
In the world of jewellery crafting, durability goes hand in hand with flexibility. Wax models must withstand the rigors of the casting process without cracking or breaking. When aimed at durability, selecting a wax that exhibits considerable flexibility is vital. For instance, a wax that is overly brittle can lead to fractures, ruining intricate work that took hours to create.
- Flexible waxes can expand under heat and contract upon cooling without losing structural integrity, making them ideal for complex designs where precision is key.
- However, if the desired effect is a more solid model, harder wax compositions might be chosen.
Durability ensures longevity in the wax model, while flexibility caters to intricate designs—two sides of the same coin in jewellery crafting.
Surface Finish and Texture
The final appearance of a wax model determines the quality of the final cast piece. The surface finish and texture of jewellery wax can hugely influence not just the aesthetic appeal but also how well the piece is received in the market.
Different waxes offer various textures:
- Smooth wax finishes are perfect for sleek designs, minimizing the need for extensive polishing post-casting.
- Textured waxes can enhance the visual complexity, allowing artisans to imprint patterns or motifs directly into the model, creating unique and eye-catching pieces.
A fine surface finish not only enhances the visual aspect but can also reduce casting defects. The smoother the mold, the less likely it is for imperfections to transfer onto the final product.
In the end, understanding these properties lays the groundwork for effective jewellery making using wax. Whether one is a novice or seasoned craftsman, grasping how to navigate through the properties of wax is fundamental in mastering the craft of gemstone jewellery.
Techniques in Wax Carving
Understanding the techniques in wax carving is crucial for anyone delving into the art of jewellery making. These methods not only define the aesthetic aspect of pieces but also ensure structural integrity for the final product. Mastery of both basic and advanced techniques can greatly influence the effectiveness of the crafting process, allowing for a smoother workflow and more intricate designs. Each approach may come with its own set of benefits and considerations. Knowing when and how to apply different techniques can elevate a jeweller's craft from ordinary to extraordinary.
Basic Carving Techniques
Starting with the basics is essential for any aspiring jewellery designer. These fundamental techniques lay the groundwork for more complex work. Key techniques include:
- Block carving: This is where the wax is shaped down from a larger piece until the desired silhouette is achieved. This basic form of carving is an excellent way to grasp proportions and dimensions.
- Incising: This technique involves making shallow cuts into the wax surface. It's often used for detailing and brings depth to designs.
- Modeling: Here, sculptural changes are made by moving wax around. This is often done with fingers or simple tools to achieve organic shapes.
Each of these basic techniques presents a unique opportunity. Learning them well sets a solid foundation for developing more advanced skills in the future.
Advanced Techniques for Intricate Designs
Once the basic skills are mastered, jewellers can explore more advanced techniques. These methods allow craftsmen to create more detailed and ornamental pieces, often incorporating complex geometrical and organic forms. Some of these include:
- Lost wax technique: Also known as investment casting, this time-honored method enables the creation of incredibly detailed designs. The wax model is encased in a mold that hardens, then the wax is melted away, leaving a cavity for metal.
- Under-cutting: This can be challenging, yet it adds remarkable depth and embellishment to designs. It involves carving away wax in ways that allow significant features to cast shadows and highlights when the piece is completed.
- Texturing: Advanced texturing techniques create surfaces that resemble natural materials or added complexities in design.
Embracing these advanced techniques enhances thematic storytelling through the jewellery. Each piece tells a story, and intricate details can enhance that narrative in impressive ways.
Utilizing Tools and Equipment
The tools and equipment employed in wax carving play an equally significant role in the results achieved. A mix of traditional and modern tools can help jewellers maximize their creative potential. Examples of important equipment include:
- Carving tools: Different shapes and sizes of blades help achieve various effects. A jeweller might use a knife for cutting and a needle tool for more detailed work.
- Heat sources: Torches or heat guns allow for quick melting and shaping of wax. Proper temperature management is essential in ensuring even melting without compromising the wax's integrity.
- Milling machines: For those looking to incorporate technology, CNC milling can produce precise designs that might be difficult to achieve by hand.
By becoming familiar with the right tools and equipment, jewellery designers can improve efficiency, precision, and overall quality in their wax carving endeavors.

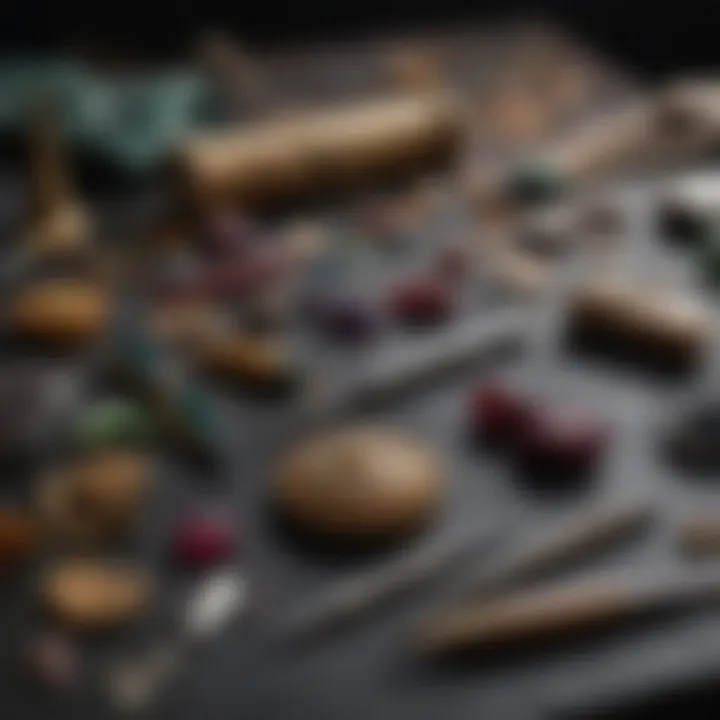
Techniques in wax carving not only shape the piece but also tell a story, connecting the craftsman to their creation in profound ways.
Investment in Wax Models
When venturing into the realm of gemstone jewellery making, the investment in wax models stands out as a crucial aspect that can define the artistry and precision of the final product. Wax models serve as the foundation upon which great pieces of jewellery are moulded, allowing for meticulous detailing and innovation in design. Let’s dive into why investing in these wax models is not just important but essential for aspiring and established artisans alike.
Advantages Over Traditional Methods
Investing in wax models brings forth a multitude of advantages when compared to traditional methods, crafting a landscape of possibilities for designers. One of the key benefits is the ease of manipulation. Wax allows for quick adjustments and modifications; a skilled artisan can carve and refine with precision that is hard to match with metal or stone at the onset. This caters especially well to the creative minds who thrive on experimentation.
Moreover, the loss of material is minimal. When making traditional castings, the process often leads to splinters or chips, which can waste valuable material. Wax, on the other hand, can be melted down and reused, making it a cost-effective choice.
However, a nuanced understanding of the benefits is paramount. Here are a few to consider:
- Detailing Capabilities: Wax can be finely detailed with tools that allow for intricate designs that would be complex to achieve in hard materials.
- Time Efficiency: The processes involved in sculpting wax models tend to require less time than traditional sculpting methods, reducing turnaround times.
- Innovative Design: The flexibility in working with wax means jewellery designers can push boundaries and explore innovative shapes and ideas effortlessly.
Indeed, these advantages make a persuasive case for using wax models throughout the design process.
Economic Considerations
From an economic perspective, investing in wax models presents both short-term benefits and long-term savings that are noteworthy. Initially, the costs associated with high-quality wax materials and tools may appear significant; however, when viewed through the lens of efficiency, the investment often pays for itself.
Using wax models, artisans can produce multiple prototypes before finalizing a design, allowing them to evaluate and tweak elements without the hefty costs of working with precious metals or gemstones prematurely. This not only saves money but also offers a margin for experimentation that leads to enhanced creative output.
Additionally, the lower production costs contribute to more competitive pricing in the market, helping jewellers attract a broader audience. Through the application of efficient methods involving wax, artisans can balance quality and affordability, thereby expanding their customer base.
"Investment in wax models not only improves the creative aspects of jewellery making but also solidifies the economic foundation required for successful crafting in today’s competitive market."
Casting Processes Using Wax Models
The art of casting processes using wax models stands as a cornerstone in the realm of jewellery creation, particularly in gemstone crafting. This method offers several critical benefits that enhance the precision and quality of the final product. Wax models allow artisans to produce intricate details that are often challenging to achieve through other techniques. The following sections delve into the particulars of the lost wax casting process and some alternatives that artisans might consider.
Lost Wax Casting Process
The lost wax casting process has been around for thousands of years, yet its importance remains undiminished. This technique involves creating a wax model of the desired jewellery piece, which is then encased in a mold made of a heat-resistant substance. Once the mold is prepped, heat is applied, causing the wax to melt away and leaving a cavity in the mold. This method provides numerous advantages:
- Exceptional Detail and Accuracy: Wax can be sculpted with extreme precision, enabling fine details that other casting methods might overlook.
- Flexibility in Design: Artisans can modify their designs easily during the modeling phase, allowing for spontaneous creativity and adaptability.
- Smooth Surface Finishes: The nature of wax lends itself to producing smooth surfaces which often reduce the need for extensive post-casting finishing touches.
"The lost wax method not only preserves the integrity of the design but also highlights the craftsmanship of the jeweller."
Once the wax is removed, molten metal is poured into the empty mold, solidifying to form the final piece. This process is not only efficient but also expresses the artist's vision more effectively than many traditional methods.
Alternatives to Lost Wax Casting
While the lost wax casting method is widely used, several alternatives exist that cater to a variety of artistic needs. Here are a few notable ones:
- 3D Printing: This modern technique allows for rapid prototyping and minimal waste. Unlike traditional methods, 3D printing can create even more complex geometries without requiring a mold. However, the strength of the final piece can vary, demanding careful material choices.
- Sand Casting: In this method, a pattern, often made from wood or metal, is placed in sand to create an impression. This technique is particularly beneficial for larger items or when working with more rugged materials. Although not as detailed as lost wax casting, sand casting can still yield powerful designs.
- Die Casting: This technique works well for mass production. The process involves injecting molten metal into a mold at high pressure. Die casting is less common in fine jewellery due to its limitations in intricate details, but for certain designs, it suits commercial needs beautifully.
Choosing the right casting method involves weighing the pros and cons based on the specific goals of each project. Each technique offers distinct possibilities and challenges that can significantly impact the end result. Understanding these processes lays the groundwork for creating jewellery that is not only beautiful but also a reflection of the craftsmanship and creativity behind each piece.
Environmental Implications of Wax Usage
The topic of environmental implications concerning wax usage in jewellery making cannot be overlooked. With the increasing awareness about sustainability and eco-friendliness in the crafting world, it's crucial to evaluate how the types of wax used can impact the environment. As gemstone enthusiasts and designers delve into their craft, understanding these aspects can guide better choices moving forward.
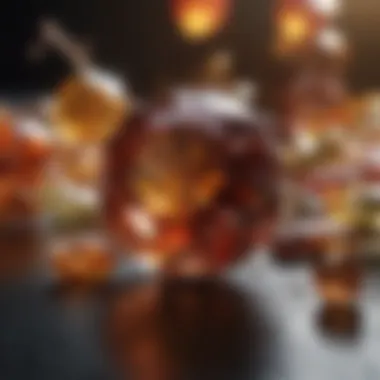
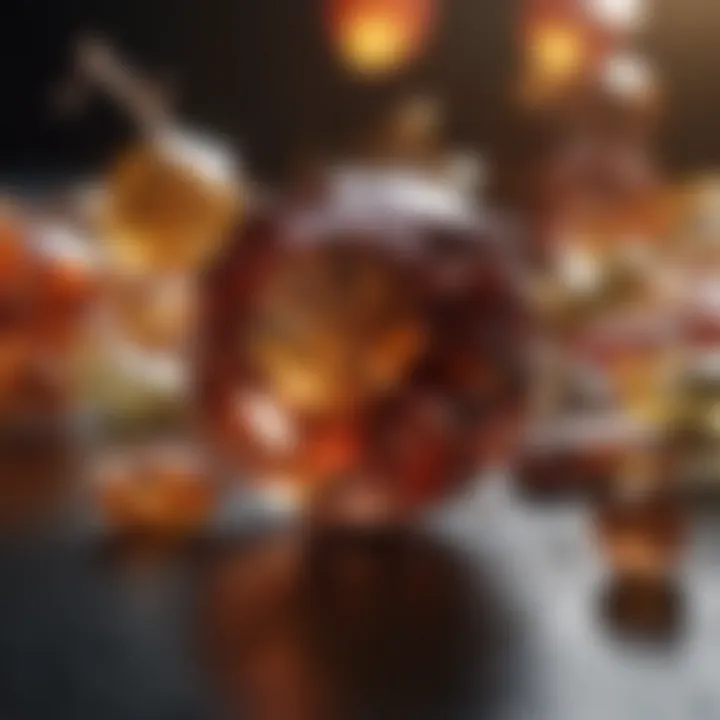
Sustainability in Wax Production
When we talk about sustainability, it covers a wide range of considerations in wax production. Certain wax types, such as beeswax and soy wax, are derived from natural sources and, compared to synthetic alternatives, they often have a lower environmental footprint.
For instance, beeswax comes from beehives and is naturally biodegradable. It supports local apiculture when sourced ethically, promoting biodiversity among pollinators which plays a crucial role in our ecosystem. On the other hand, paraffin wax — a byproduct of petroleum — raises a few eyebrows due to its fossil fuel origins and the environmental consequences tied to oil extraction. As more artisans seek to minimize their negative impact, the shift toward sustainable materials becomes not just a trend, but a responsibility.
Additionally, producers who prioritize eco-friendliness often employ ethical methods in sourcing and refining their materials, ensuring less harm to the environment. This includes using renewable energy sources during the production process or implementing waste reduction strategies. Consumers and designers alike can significantly contribute to environmental preservation by choosing to incorporate these sustainable alternatives in their projects.
Recycling and Waste Management
The recycling aspect of wax usage in jewellery production presents a pathway to minimize waste and promote sustainability. Indeed, leftover wax from carving processes is often seen as waste, but this can be mitigated through innovative recycling methods.
- Repurposing: Unused wax scraps can be melted down and reshaped for new projects. This minimizes waste and offers designers unique materials for future pieces.
- Reusing: Some artists create sample models or practice pieces, utilizing leftover wax, ensuring that every bit counts.
- Disposal: Proper management of wax disposal is essential. Rather than throwing it in the landfill, many workshops are beginning to adopt recycling programs specifically managing wax waste.
"When we rethink our methods and embrace recycling, the waste that once seemed burdensome transforms into opportunities.
Future Trends in Jewellery Wax
The world of jewellery wax is not just about tradition and established practices; it is also a dynamic field influenced by emerging trends that reshape how artisans create and innovate. Understanding these future trends in jewellery wax is vital for anyone involved in gemstone crafting, from creators to collectors. As we look ahead, several specific elements stand out, emphasizing the importance of adaptability and foresight in this art form.
One of the most significant shifts is the increasing emphasis on sustainability. As the world becomes more environmentally conscious, the demand for eco-friendly materials has surged. Wax formulations derived from renewable resources are making headway, and this trend not only promotes responsible crafting but also appeals to a clientele that values sustainability in their purchases.
Moreover, advancements in formulation technology mean that wax can now be engineered to have better workability and performance. This includes improved melting points and enhanced durability, making the crafting process smoother and more efficient. Artisans can now create more intricate designs with minimal effort, reflecting the balance between artistry and practicality.
"As the craftsmanship of jewellery evolves, so too must the materials we use. Embracing innovation is crucial for the future of jewellery making."
Another important factor is the integration of technology into the casting techniques. The tools of today not only enable artisans to produce intricate designs with precision but also streamline the overall casting process, reducing waste and increasing efficiency. With 3D printing technology gaining traction, we see a blend of traditional wax models with modern digital techniques. This fusion allows for rapid prototyping and can significantly cut down on production times.
In essence, the future trends in jewellery wax encapsulate a shift towards more sustainable practices, advanced formulations, and the incorporation of technology within traditional methods. As these elements evolve, they promise to enhance the skill and creativity of artisans, ultimately transforming how gemstone jewellery is crafted and appreciated.
Innovations in Wax Formulations
Innovations in wax formulations are paving the way for a new era in jewellery making. Traditional waxes, while effective, often come with limitations in terms of flexibility and usability. Modern chemists and artisans are collaborating to develop hybrid waxes that combine the best properties of various materials. For instance, formulas that blend natural and synthetic components can provide superior thermal stability and a finer finish.
Furthermore, the enhancements in additives allow for a wider range of finishes, from matte to gloss, without the need for additional treatment. These innovations not only elevate the aesthetic appeal of the final product but also increase the functional aspects, like resistance to cracking and improved detail reproduction.
Technological Advances in Casting Techniques
The landscape of casting techniques is also undergoing a transformation, significantly affecting how wax models are used in jewellery creation. The advent of computer-aided design (CAD) systems allows artisans to create highly detailed digital models, which can then be realized in wax with astonishing precision using 3D printing technology. This advancement means that intricate designs that once took days or weeks can now be produced within hours.
Moreover, lost wax casting, the traditional hallmark of jewellery production, is enhanced with more efficient melting and pouring processes. Techniques that minimize air pockets not only improve the integrity of the final piece but also reduce material waste—an essential consideration in today's market.
Epilogue
As we wrap up our exploration of jewellery wax within the context of gemstone crafting, it’s essential to understand the multifaceted role it plays in the entire process. This article has delved into various aspects of jewellery wax, from its types to casting methods, and its environmental implications. But perhaps what stands out most is its unparalleled flexibility in design and production.
Recap of Key Insights
Throughout this piece, we've illuminated several significant points about jewellery wax:
- Types of Waxes: Each wax type carries its unique properties, such as melting points and texture, catering to different crafting needs.
- Crafting Techniques: The techniques discussed, whether basic or advanced, have shown how wax carving serves as a bridge between raw creativity and refined craftsmanship.
- Environmental Considerations: The sustainability discussion highlights how the industry is moving toward eco-friendly practices, factoring into purchasing decisions.
- Paraffin-based waxes offer versatility.
- Carnauba wax provides a natural sheen.
- Specialty waxes are tailored for intricate works.
This broader perspective not only emphasizes the technical aspects but also the continuing evolution of the craft.
The Enduring Importance of Jewellery Wax
Jewellery wax remains at the core of gemstone crafting for reasons beyond mere utility. Its significance can be highlighted through these points:
- Innovation in Design: The ability to mold wax allows designers to push boundaries, creating one-of-a-kind pieces that might be difficult or impossible to achieve with traditional methods.
- Economic Viability: The cost-effectiveness of using wax in the early stages of jewelry creation significantly impacts the final product, influencing pricing structures in the market.
- Cultural Relevance: As artisans around the globe continue to adopt wax techniques, it helps preserve age-old traditions while blending in modern innovations.