Understanding Wax Loss Casting in Gemstone Jewelry
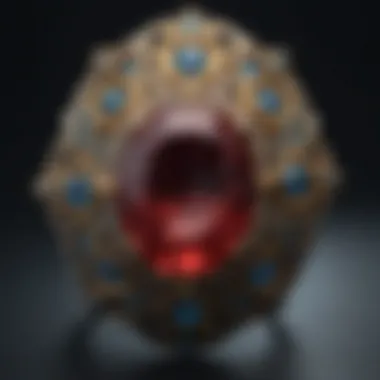
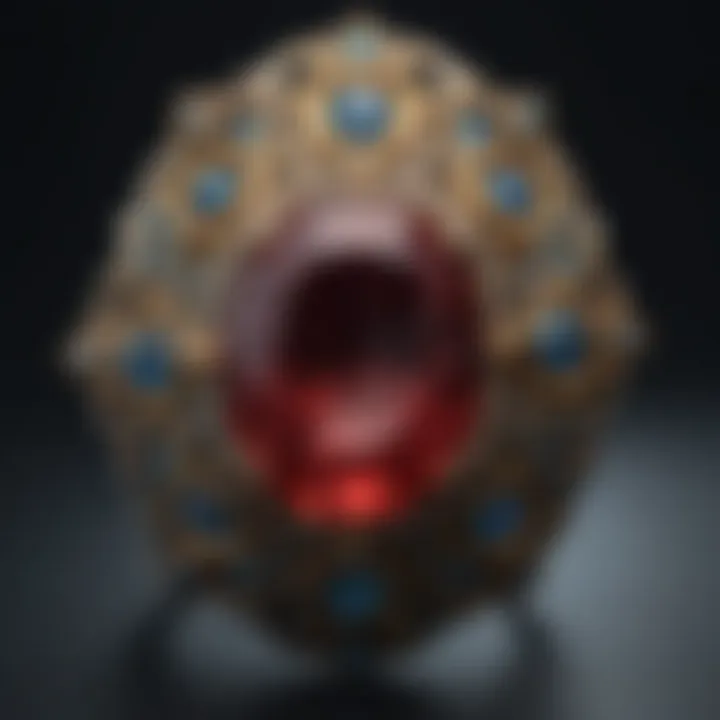
Intro
In the world of gemstone jewelry, wax loss casting stands as a cornerstone technique, blending artistry and science in the creation of intricate designs. The process not only offers jewelers the ability to manipulate forms with precision but also plays a vital role in preserving the brilliance of the gemstones involved. From ancient practices to modern innovations, this method has evolved while retaining its core significance in craftsmanship.
This article will take you on a journey through the historical foundations of wax loss casting, examining how it paved the way for the sophisticated designs we appreciate today. We’ll explore the materials and methods that artisans employ, delve into the benefits of this technique, and discuss how it remains relevant in today’s jewelry landscape. By the end, whether you’re a jeweler or a gemstone aficionado, you’ll gain invaluable insights into the art and science of this essential casting technique.
Gemstone Overview
When discussing wax loss casting, it’s crucial to understand the gemstones that are often involved. These precious stones not only add beauty but also hold unique properties that influence the overall design of the jewelry.
Description of the Gemstone
Gemstones, such as sapphires, emeralds, and rubies, start as raw materials found in nature. Each stone undergoes a rigorous process of cutting and polishing before reaching its final form. The allure of gemstones lies not only in their aesthetic appeal but in their cultural significance and history.
Physical Properties
- Hardness: Measured on the Mohs scale, hardness affects durability. For instance, diamonds, rated a 10, are incredibly tough, while softer stones like opals rate around 5.5 to 6.5.
- Color: A pivotal aspect of how gemstones are priced and valued, where even slight variations can lead to notable differences in appeal.
- Clarity: Refers to the presence of inclusions or blemishes; clearer stones generally command higher prices.
- Cut: Affects how light interacts with the gem, influencing brilliance and sparkle.
Understanding these properties helps jewelers select the right gemstone for their projects, ensuring that the final product stands as a testament to both beauty and durability.
Healing Properties
Beyond their physical attributes, gemstones are often celebrated for their metaphysical qualities. Many believe that specific stones carry unique healing energies.
Metaphysical Attributes
- Amethyst: Known for its calming energies, often used to promote tranquility.
- Rose Quartz: Frequently associated with love and emotional healing, making it popular in various jewelry forms.
- Citrine: Said to bring joy and optimism, often referred to as the “merchant’s stone” for its supposed ability to attract wealth.
These attributes resonate with individuals interested in the holistic aspect of gems, making them not only decorative items but also tools for personal growth and healing.
Common Uses in Holistic Practices
Jewelry designers often draw from these properties, incorporating gemstones into pieces aimed at enhancing personal well-being or to complement spiritual practices. Besides adornment, gemstones may be utilized in meditative practices, energy work, and even Feng Shui.
"Understanding the combination of physical and metaphysical properties of gemstones can elevate both the artistry and functionalism of jewelry designs."
Understanding Wax Loss Casting
Understanding wax loss casting is crucial in grasping the intricate relationship between technique and artistry in gemstoned jewelry. This method not only shapes the physical form of the jewelry, but it also unveils the narrative behind each piece. Wax loss casting essentially merges age-old craftsmanship with modern design, allowing jewelers to realize their most imaginative visions while maintaining precision. It holds numerous advantages, including fine detail, versatility, and efficiency, which makes it a staple among skilled artisans and enthusiasts alike.
Definition and Overview
Wax loss casting, often known simply as lost wax casting, is a method where a wax model is created and encased in a material that hardens. Once the casing is set, the wax is melted away, leaving a hollow mold into which metal is poured. This technique allows for intricate designs that are otherwise challenging to achieve with traditional methods. The molds can capture fine details, which is essential in jewelry design, where even the smallest marginal errors may affect the final look.
Historical Background
Ancient Origins
The roots of wax loss casting can be traced back to ancient civilizations, notably in cultures such as the Chinese and the Egyptians. This age-old process demonstrates a key characteristic: its ability to produce detailed objects that were both functional and decorative. Craftsmen relied on this technique to create intricate jewelry and ritualistic artifacts, where every curve and line told a story or reflected beliefs. The use of wax loss casting in ancient times not only speaks to its enduring popularity but also highlights its effectiveness in opening up new avenues for artistic expression. One of the distinct advantages of this method was that it allowed for multiple copies of a single design, which meant that artisans could cater to a wider audience while preserving the quality and style of their work.
Evolution Through the Centuries
As the centuries rolled on, the practice of wax loss casting adapted and transformed, aligning with advancements in metallurgy and design. For example, during the Renaissance, the technique saw a resurgence as artists began to explore and push the envelope of creativity and complexity in their designs. A hallmark of this evolution is its integration into diverse jewelry making styles. Jewelers in Europe, Middle East, and Asia all experimented with local materials, resulting in unique adaptations. The lasting benefit of this evolution lies in how it has enriched the craft, allowing jewelers to adopt best practices from around the globe while still adhering to traditional roots.
Wax Casting in Different Cultures
Wax casting has also found a prominent place in various cultures, marking its significance in regions like Africa and India. In these areas, artisans crafted not just jewelry, but also ceremonial items and religious artifacts. The beauty of this technique, when viewed cross-culturally, lies in its ability to effortlessly merge different materials and motifs, meeting local aesthetic preferences. Each culture's unique approach brings forth a rich tapestry of designs that celebrate both tradition and innovation. For example, African craftsmen often use bright colors and bold designs, showcasing a breadth of creativity that continues to inspire contemporary jewelers today. This cultural intersection allows for a greater appreciation of the medium, opening doors for future artists to blend traditions, thereby expanding the realm of possibility in jewelry design.
"Wax loss casting is not just a technique; it is a bridge connecting artisans with their history, culture, and creativity."
In essence, understanding wax loss casting involves recognizing its deep historical context and the multi-faceted attributes it exemplifies in today’s jewelry making. This foundational knowledge paves the way for both appreciation and innovation in the craft.
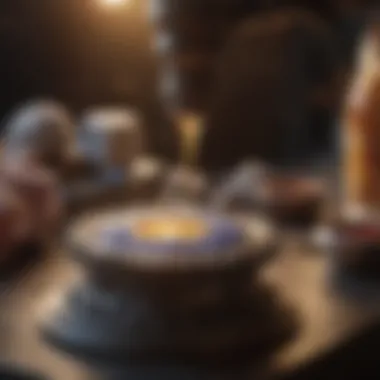
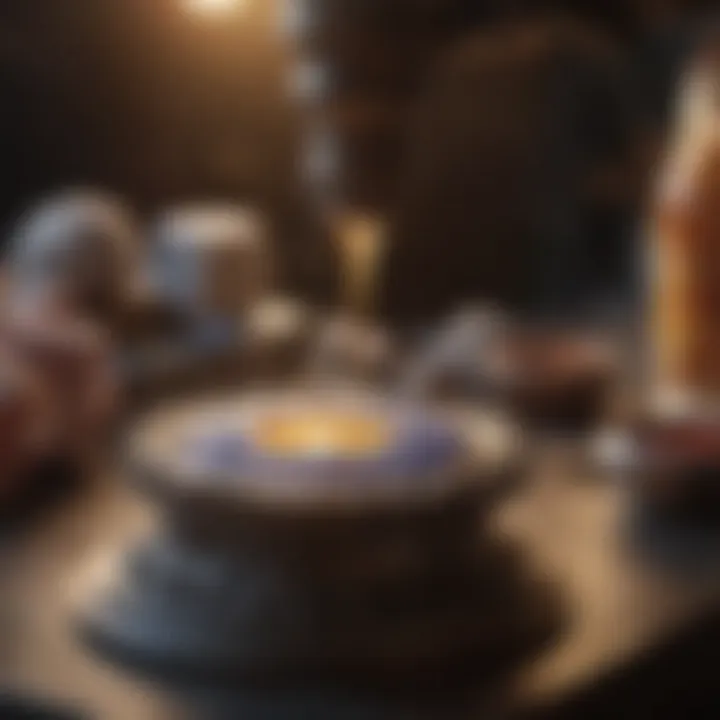
Technical Aspects of Wax Loss Casting
The technical intricacies of wax loss casting play a pivotal role in the creation of exquisite gemstone jewelry. The method, often regarded as an art form as much as a scientific endeavor, relies on several critical components that contribute to its overall effectiveness and finesse. From the materials employed to the precision steps of the casting process, each aspect is essential in shaping the final product. Factors such as the types of wax, investment materials, and metal alloys significantly influence how well the detailing and craftsmanship are maintained throughout the process.
Materials Used
Types of Wax
When it comes to crafting wax models, the selection of wax is far from trivial. Various materials can be utilized, but the most favored are typically paraffin and thermoplastic waxes. Paraffin wax is widely appreciated for its ease of melting—a straightforward characteristic that speeds up the initial phases of model creation. Likewise, thermoplastic wax offers exceptional adaptability. This makes it a beneficial choice since artists can reshape it multiple times without significant structural loss. Nonetheless, a downside is that some wax types can produce more residual soot during the burnout process, impacting the overall cleanliness of the casted piece.
Investment Materials
Investment materials are integral to the durability and resilience of wax loss casting. Gypsum-based investments are common due to their capability to withstand high temperatures without crumbling. They ensure that delicate details of the molten metal are captured crisply. This characteristic is crucial for jewelers who prioritize clarity and definition in their designs. However, it’s worth noting that investment materials can sometimes lead to longer curing times, which might be a hurdle for those looking for quicker production cycles. On the flip side, the quality achieved through proper investment is often deemed worthwhile.
Metal Alloys
The choice of metal alloy is another critical consideration with wax loss casting. Silver and gold alloys tend to dominate the market given their beauty and durability. Each alloy presents its own set of benefits; for instance, gold alloys can provide varied shades, which open avenues for customization. The material’s melting point and conductivity, also, are determining factors in how smooth the pouring process will be. Sometimes, though, lower-quality alloys might present challenges such as tarnishing or even difficulty in achieving the desired finish, which can frustrate craftsmen.
The Casting Process
Creating the Wax Model
The first step in the casting process involves crafting a wax model that will serve as the template for the final product. This initial phase is a blend of art and technique—the designer must ensure that every intricate detail is carefully sculpted. By doing so, they lay the groundwork for achieving a high-quality finished piece. The defining advantage here is the control artisans have over the model's exactitude, allowing for personalized adjustments. However, missteps in this phase can result in irreversible errors, affecting the entire batch.
Investment and Curing
Next comes the investment and curing stage, wherein the wax model is encased in the chosen material. A meticulous approach is required to eliminate air bubbles that can mar the surface once the metal is poured. The curing phase allows the investment to gain its strength, ensuring it can withstand the heat when the wax is melted away. This step sounds simple, yet it requires patience. Curing times vary depending on the material—sometimes extending to several hours—which can pose a challenge for designs with tight deadlines, yet ensuring a properly cured mold is non-negotiable for quality.
Wax Removal Techniques
Removing the wax is a critical and delicate stage, which typically comes after the investment has fully hardened. A common approach is applying heat through the use of a kiln to melt away the wax, leaving behind a hollow investment shell, ready to be filled with molten metal. The precision of this step is vital. If done hastily, there's a risk of damaging the investment mold, leading to unforeseen costs and time delays. Nonetheless, mastering wax removal techniques can greatly enhance the overall efficiency and effectiveness of the entire casting operation.
The technical aspects of wax loss casting allow for a stunning blend of art and science, making it an enticing pursuit for jewelry artisans.
Advantages of Wax Loss Casting
Understanding the advantages of wax loss casting is crucial for anyone keen on gemstone jewelry making. This method not only brings out high precision in designs but also offers versatility, making it a favorite among jewelers. It's like having a Swiss Army knife at hand; it's not just useful, but indispensable in the jewelry craft.
Precision and Detail
One of the standout qualities of wax loss casting is the precision it affords. Jewelers can replicate minute details that would be virtually impossible to achieve with traditional methods. By creating wax models, artisans can fine-tune every curve and contour before the final casting. Once the wax is melted away, what's left is a mold that mirrors the original design exquisitely.
This precision is crucial especially when it comes to setting gemstones. A well-crafted mold ensures that each stone fits snugly, enhancing not only the aesthetics but also the durability of the piece. For instance, when a jeweler wants to set a diamond into a ring, there’s a substantial difference between a loose or poorly fitted stone and one that sits tight in its setting. This meticulousness in detail minimizes the risk of future wear and tear, safeguarding the jewelry’s longevity.
Versatility in Design
Wax loss casting is noted for its adaptability, allowing designers to think outside the box. The technique caters not just to traditional shapes but opens doors for modern and intricate designs that push boundaries. This versatility stems from the malleability of wax itself. Jewelers can easily sculpt complex patterns or combine different designs within a single casting.
For example, a designer envisioning a dragonfly motif can seamlessly integrate delicate wings alongside gemstones, crafting an extraordinary piece that tells a story. Additionally, this casting technique can accommodate various sizes, textures, and combinations of materials, which is invaluable for custom-designed pieces. With this flexibility, each piece of jewelry can be unique, satisfying the desires of both the designer and the end customer.
Cost-Effectiveness
In today's fast-paced world, cost considerations play a vital role in production. Wax loss casting, despite its luxury connotation, can be quite cost-effective in the long run. Initially, setting up the process might require some investment in materials and equipment. But, once the molds are created, jewelers can mass-produce items at a fraction of the cost.
Furthermore, the elimination of certain post-production processes, like extensive polishing or extensive adjustments, can also save time and resources. It reduces waste in terms of excess materials and labor. This is an appealing factor for newer designers who are adept at maximizing resources while still ensuring quality.
"In the realm of gemstone jewelry, precision, versatility, and cost-effectiveness are not just added benefits; they are the cornerstone of craftsmanship that delivers excellence."
In summary, the advantages of wax loss casting resonate deeply within the gemstone jewelry community. Artists can achieve unmatched precision, tap into vast design flexibility, and maintain a keen eye on costs—all while producing stunning, timeless pieces.
Challenges and Solutions
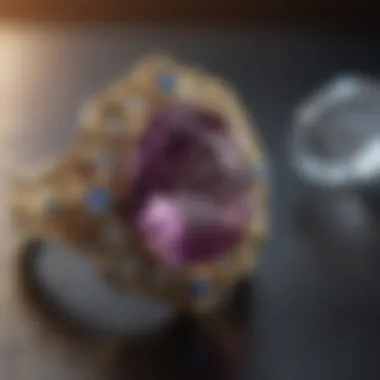

When delving into the art of wax loss casting, one cannot ignore the hurdles craftsmen face. Addressing these challenges is not only essential for successful outcomes but also fosters innovation in the jewelry-making process. From achieving the desired precision to maintaining structural integrity, understanding these hurdles gives artisans and enthusiasts a critical edge.
Common Issues in Wax Loss Casting
Model Shrinkage
Model shrinkage is a natural adversary in the casting process due to the cooling of materials. As the wax model transitions from its warm, malleable state to a solid, molded counterpart, it contracts. The key characteristic of model shrinkage lies in its predictability: it typically occurs in all types of wax utilized in this method. While shrinkage is an inherent aspect of various casting processes, in wax loss casting, the challenge represents both risks and opportunities.
One specific aspect contributing to model shrinkage is the temperature variance during the cooling process, which may cause gemstones to misalign or appear disproportionate. If not handled with care, this contraction can lead to significant discrepancies in the final piece, impacting its aesthetic and structural integrity.
Despite these challenges, model shrinkage is sometimes viewed as a beneficial aspect, as it allows for minor adjustments during the design phase. Uniquely, it invites artisans to create slightly larger models knowing they will contract. This advantage, however, comes with a caveat. Proper measurements and adjustments are critical to ensuring the finished product aligns with the artist's vision, making it a double-edged sword in the creation of gemstone jewelry.
Investment Cracking
Investment cracking occurs when the material surrounding the wax model fails due to improper curing or temperature fluctuations. This issue can wreak havoc on an otherwise flawless casting journey. The primary culprit often stems from inadequate mixing ratios of investment materials or insufficient curing time, leading to surface faults that compromise the entire design.
Investment cracking can be particularly detrimental as it impacts the outer shell of the mold, which should ideally capture every fine detail of the original design. The disadvantage here is clear: defects in the mold translate to flaws in the finished item. Yet, understanding how to combat this issue can turn challenges into learning experiences.
By employing better investment techniques, such as ensuring the mix is properly blended or using vacuum techniques to remove air pockets, artists can significantly mitigate the risk of investment cracking. This specific knowledge makes it a focus point within the narrative of improving overall casting practices.
Metal Pouring Errors
Metal pouring errors represent another critical hurdle encountered in the casting process, particularly when introducing molten metals into the investment mold. Variations in pouring speed, temperature, or even the metal quality can lead to incomplete fills, resulting in missing sections or poorly defined details in the final product. The intricacies involved in this operation must not be understated, as even the slightest oversight can lead to significant mishaps.
One noteworthy characteristic of metal pouring errors is their variability. Factors such as the viscosity of the molten metal and ambient temperature can greatly affect pour quality. Moreover, a unique aspect of this challenge is its propensity to occur unexpectedly, catching some artisans off guard. The advantage is that with practice, an artisan can develop a keen instinct for recognizing the pivotal conditions needed for optimal pouring, constructing a more reliable process.
Techniques for Overcoming Challenges
Navigating these challenges requires a toolkit of strategies tailored for resilience and assurance throughout the casting journey. Some effective techniques include:
- Thorough Preparations: Conducting feather-light practices in model crafting can help minimize shrinkage.
- Effective Mixing Techniques: Invest in high-quality mixing tools and invest time to perfect the ratios that drastically improve investment quality.
- Temperature Control: Adapting protocols for both wax models and metal pouring to maintain consistent thermal environments.
Armed with these strategies, the experienced craftsman ensures a smoother pathway through the intricate world of wax loss casting, ultimately enhancing both skill and artistry in gemstone jewelry creation.
"Challenges may test one's patience, but they also refine our craftsmanship. Each error is an opportunity for growth and mastery in the art of casting."
Ultimately, the journey through challenges is what molds a proficient artisan, leading to extraordinary creations in the world of gemstone jewelry.
Innovations in Wax Loss Casting
The field of gemstone jewelry making is continuously evolving, and innovations in wax loss casting play a huge role in keeping artisans ahead of the curve. The creativity and precision that this casting method offers are completely revolutionized by recent technological advancements and sustainable practices. These innovations are not just trends; they significantly enhance the overall quality and appeal of the jewelry produced. As we dive into this section, we’ll shed light on some pivotal developments in this area, focusing on how they contribute to the larger jewelry-making landscape.
Technological Advancements
3D Printing Integrations
One of the most exciting areas of development is the integration of 3D printing into the wax loss casting process. This modern technology allows jewelers to create intricate designs that were previously hard to accomplish with traditional methods.
The key characteristic of 3D printing is its ability to produce highly detailed wax models quickly, minimizing the time from concept to finished product. This is a beneficial choice for artisans who need flexibility in their designs and often need to meet client demands swiftly.
What sets 3D printing apart in this realm is its capacity for customization. Jewelers can design unique pieces tailored to individual preferences without the constraints of standard molds. This can dramatically attract clientele looking for bespoke solutions.
However, it does come with some disadvantages. For instance, while the technology can create complex designs, the initial investment in equipment can be significant. Furthermore, there may be challenges in achieving the same finish that traditional hand-carved models can offer, which might be important for high-end pieces.
Computer-Aided Design (CAD) in Wax Models
Another leap forward is the use of Computer-Aided Design (CAD) in creating wax models. This digital design approach allows jewelers to visualize and manipulate their designs more effectively before they commit them to wax.
The primary appeal of CAD is its precision. It enables artisans to generate exact dimensions and fine details that are often crucial in jewelry making. This is especially important in maintaining symmetry and ensuring that gemstones are set securely within the design.
Using CAD also opens the door to easy modifications. Jewelers can quickly adjust designs based on customer feedback, reducing the potential waste of materials before the casting process even begins. While CAD is generally seen as a valuable asset, it might present a learning curve for those used to traditional design methods. Moreover, overly complex designs may occasionally result in challenges during casting, leading to potential errors that require additional time to rectify.
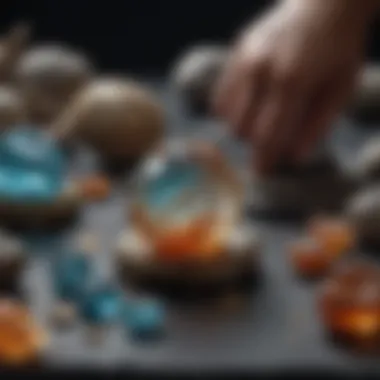
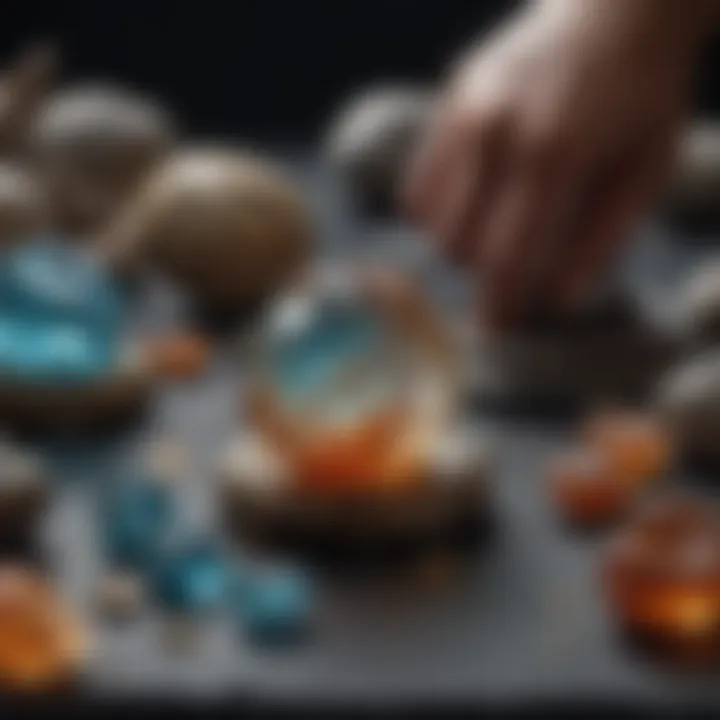
Sustainable Practices
Eco-Friendly Materials
A shift toward sustainability is evident in the materials being used for wax casting. Eco-friendly materials are increasingly making their mark, allowing jewelers to create stunning pieces while being kind to the planet.
The standout feature of eco-friendly materials is that they often come from renewable sources or are biodegradable. This characteristic is important as it reduces the ecological footprint of the jewelry production process. As consumers are more eco-conscious, integrating these materials can also enhance a brand's appeal and marketability.
While the main advantage is the ethical aspect, one must also consider that not all eco-friendly materials achieve the same level of detail or finish as traditional wax. Jewelers might need to experiment to find the right balance between sustainability and the high standards of craftsmanship expected in fine jewelry.
Reducing Waste in the Casting Process
Lastly, there's a growing focus on reducing waste in the casting process itself. The challenge of minimizing leftover materials while optimizing production is steadily gaining traction.
The essence of reducing waste lies in smarter planning and precise designs that leave little to no excess material after the casting stage. This is particularly appealing for jewelers who are aware of cost implications and want to maximize profits without compromising their environmental commitments.
However, implementing waste-reduction strategies calls for careful training and adaptation. Jewelers must be mindful of their processes and continuously evaluate them to achieve this efficiency, which can be resource-intensive initially.
"Innovations in wax loss casting not only streamline the production process but also pave the way for more sustainable and personalized jewelry, reflecting modern consumer values while keeping tradition alive."
In summary, the innovations in wax loss casting are shaping the future of gemstone jewelry. They offer artisans tools that enhance creativity while factoring in sustainability – crucial elements for today’s discerning consumers.
The Impact of Wax Loss Casting on Gemstone Jewelry
The practice of wax loss casting bears significant weight in the world of gemstone jewelry. This technique not only transforms how artisans approach jewelry design but also shapes the very foundations of gemstone aesthetics. Understanding its impact is crucial, as it allows both creators and admirers to appreciate the intricate dance between craftsmanship and artistry.
Influence on Gemstone Setting
Wax loss casting has revolutionized gemstone setting by offering a seamless integration of metal and stone. Traditional settings often required invasive procedures or bulky frameworks, but with this modern technique, jewelers can design more intricate and delicate settings. The precision achievable allows stones to sit snugly, secured without compromising their beauty. This method provides flexibility in the design, enabling unique settings that can highlight the gem’s brilliance.
Craftsmanship shines in knowing how to balance visibility and stability in these designs. For example, a setting created using wax casting might feature a filigree-style surround, allowing maximum light exposure to a dazzling diamond, showcasing its sparkle like never before. The effect is pleasing to the eye, a delicate embrace of metal around the stone, rather than overshadowing it.
Enhancing the Visual Appeal of Jewelry
Visual allure is at the core of gemstone jewelry, and wax loss casting amplifies this characteristic in countless ways. By utilizing advanced techniques, artisans can experiment with forms and textures that were previously impractical. The wax model's detail often translates beautifully in metal, preserving even the minutest intricacies that evoke emotions and tell stories.
Consider a piece designed for a special occasion—a ring adorned with colored gemstones. Through wax casting, the designer can create a flowing band that captures the essence of natural elements, perhaps mimicking waves or petals. Such careful consideration enhances not only the aesthetic appeal but also evokes feelings tied to nature or emotions, setting each piece apart as a personal statement.
"The beauty of jewelry lies not just in its materials but in the stories it tells through its design and craftsmanship."
The Role of Craftsmanship
At the heart of wax loss casting is craftsmanship; a marriage of skill and artistic vision. Craftsmanship is more than mere technique; it embodies the passion and attention to detail that artists pour into their works. Each wax model is a tactile representation of an idea, reflecting the creator’s intent before it even meets molten metal.
The artist's hand is evident in the casting process. A skilled artisan knows how to manipulate materials—understanding how the metal will behave once it is poured or how the wax will burn away. This knowledge allows for the creation of pieces that endure through time, blending functionality with beauty. Craftsmanship also encompasses the iterative process of refining a design, ensuring that each piece is not just jewelry, but a wearable work of art.
In this dance of materials and aesthetics, wax loss casting has significantly shaped the landscape of gemstone jewelry, offering endless possibilities for creativity while enhancing both form and function.
Closure and Future Directions
The Conclusion and Future Directions of wax loss casting in gemstone jewelry serves as a crucial juncture, tying together insights gleaned throughout the article while also peering into the horizon of this remarkable technique. This section not only synthesizes the information on historical context, materials, and processes but also contemplates the evolving landscape of jewelry making in an increasingly technological age.
This technique, rooted in tradition, offers a bridge to modern advancements. Understanding where it stands today empowers jewelers and enthusiasts alike to appreciate the artistry involved. Moreover, the exploration of future directions invites readers to consider their role in pushing boundaries through innovation.
Summary of Key Points
Throughout this article, we explored several pivotal elements of wax loss casting that characterize its place in the gemstone jewelry world. Here are the key points:
- Historical Context: A deep dive into the origins and evolution, showcasing its cultural significance across various societies.
- Materials and Techniques: Details on types of wax, metal alloys, and investment materials used in creating stunning pieces.
- Advantages and Challenges: The precision and versatility offered by wax loss casting, alongside common difficulties faced by artisans.
- Innovative Practices: Incorporation of technology and sustainability in modern approaches.
- Impact on Aesthetics: How this method enhances the visual appeal of gem settings and serves as a canvas for exceptional craftsmanship.
Evolving Trends in Jewelry Making
The realm of jewelry making is ever-changing. As artisans adapt to new inspirations and tools, we see exciting trends emerging.
- Integration of Technology: Advancements like 3D printing and CAD software have transformed the design process, allowing for unprecedented precision and creativity in wax models.
- Sustainability Focus: There is a notable shift towards eco-friendly practices. Jewelers are keen on using materials that minimize environmental impact, ensuring that the beauty of creation does not come at the expense of our planet.
- Cultural Reflections: A growing appreciation for designs that draw from global influences. Jewelers are channeling diverse heritages, integrating unique styles that appeal to a broad audience.
- Personalization: The demand for custom pieces is on the rise. Individuals seek meaningful creations that tell their stories, leading artisans to innovate in how they approach design and customer engagement.
The future shines promisingly for wax loss casting in the world of gemstone jewelry, where the blend of tradition and progress invites endless possibilities.