Exploring the Essentials of Jewelry Casting Supplies
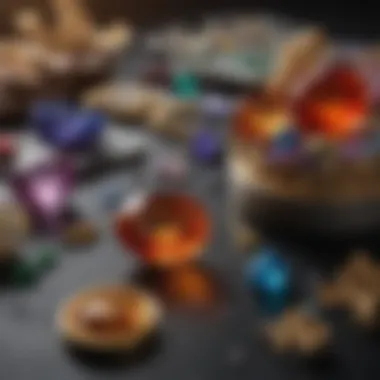
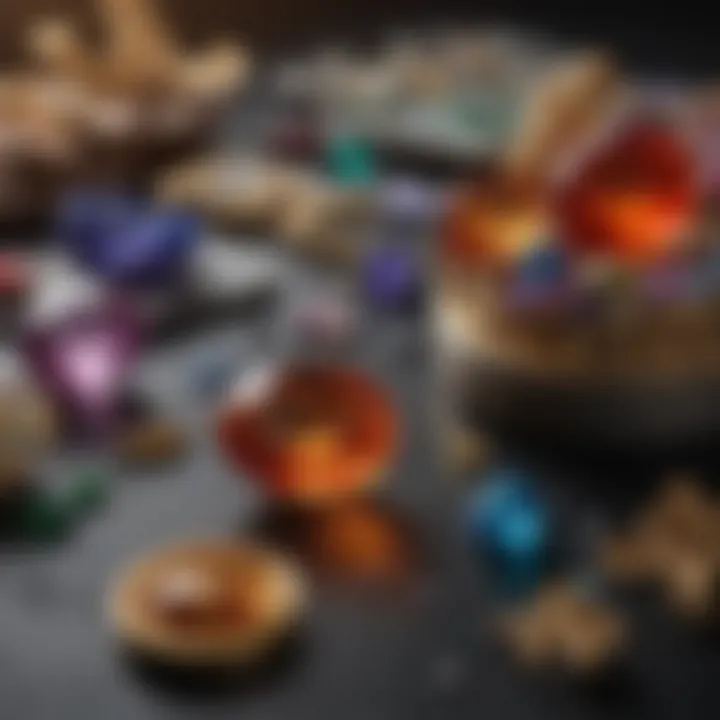
Intro
Creating jewelry is an art form that marries creativity with precision. At the heart of this craft lies the understanding and mastery of casting techniques. From metals to molds, each component plays a crucial role in shaping a piece from mere concept into a stunning final product. Whether a seasoned artisan or a budding enthusiast, every jeweler must choose their casting supplies wisely to achieve their vision.
Casting is not just about melting metal; it’s a detailed process that involves an array of materials and tools. For example, consider the quality of wax: a cheap option can create problems down the line, spoiling the final piece. What about the molds used in this process? The choices can range from simple silicone molds to elaborate ceramic ones, each impacting the outcome significantly. Therefore, understanding these materials is essential for any jewelry maker.
This article aims to provide an insightful look into the world of jewelry casting supplies. It seeks to illuminate various processes, spotlight innovative tools, and discuss the increasing relevance of sustainability within the jewelry industry. A comprehensive grasp of these elements will not only elevate one’s technical skill but will also enhance the appreciation of the art form itself.
Understanding Jewelry Casting
Jewelry casting stands at the intersection of artistry and craftsmanship in the world of adornment. Understanding this process is crucial not just for jewelers, but for gemstone enthusiasts and collectors who appreciate the finesse of handcrafted jewelry. Casting is more than a mere technical procedure; it embodies creativity and tradition, transforming raw materials into unique masterpieces.
Taking a closer look, casting allows jewelers to replicate intricate designs effectively. This method is impeccable for creating detailed pieces that could be painstaking to craft by hand. Thus, it plays a pivotal role in mass production and custom orders alike. By streamlining the creation process, casting opens the doors for designers to explore innovative styles and fresh ideas, ultimately advancing the craft itself.
Definition and Purpose
Jewelry casting involves pouring molten metal into a mold and allowing it to solidify, resulting in a finished piece. This method serves multiple purposes: it is a way to produce jewelry that maintains high levels of detail and can be reproduced consistently. This means that whether you’re crafting a single, bespoke piece or running a larger batch production, jewelry casting can accommodate diverse needs.
To break it down further, there are different types of casting techniques such as lost-wax casting, die casting, and centrifugal casting. Each method has its nuances and advantages, making it essential for jewelers to understand when and how to employ each technique. The interplay of metal types, wax models, and mold materials is crucial in this craft, as it directly impacts the quality and integrity of the final product.
Historical Context
The roots of jewelry casting reach back thousands of years, hinting at the evolution of human creativity and technology. The process likely originated in ancient civilizations, where artisans first employed simple molds to shape metal into ornaments and tools. Early examples can be traced to the Egyptians, who crafted hierarchical masterpieces often buried with their pharaohs.
In the Middle Ages, advancements in metalworking gave rise to more sophisticated methods. Lost-wax casting, particularly, gained prominence during this era. Jewelers began to replicate intricate designs with a finesse that had not been achieved before, paving the way for the stunning pieces we see today.
The industrial revolution marked another significant leap. Mass production practices emerged, allowing jewelry to be more accessible. However, this rapid production sometimes sacrificed artistry for quantity—a trade-off that many artisans today seek to balance by returning to traditional, hand-crafted techniques combined with modern technology.
Understanding this rich historical context helps new and seasoned jewelers alike appreciate the craftsmanship involved. By knowing where the craft comes from, artisans can infuse their work with more intention and depth, making for a richer experience in both creation and appreciation.
"The beauty of jewelry casting lies not just in the finished piece, but in the narrative of its creation."
Through understanding jewelry casting—its definition, purpose, and historical significance—both jewelers and enthusiasts can grasp the magnitude of what it takes to turn a vision into tangible beauty. This knowledge plays a critical role in encouraging further exploration and innovation within the craft.
Essential Jewelry Casting Supplies
In the fascinating world of jewelry making, the right supplies serve as the foundation for both quality and creativity. Essential jewelry casting supplies are more than just tools; they are the building blocks that allow artisans to transform their visions into tangible pieces. Understanding what these supplies are and how they function can streamline the process, making it smoother and more efficient, not to mention elevating the final product.
Not only do these supplies impact the quality of the casting, but they directly influence the overall efficiency of the jewelry-making process. When it comes to production, having reliable equipment means fewer errors and enhanced safety. Novices and seasoned jewelers alike need to pay close attention to the details, selecting the right materials to match their specific requirements and style. Here, we dive into a comprehensive discussion of the tools necessary for successful jewelry casting, starting with the melting equipment, which is where the journey begins.
Melting Equipment
Melting equipment is paramount in the jewelry casting process. This is where metal in its solid form transitions to liquid, ready to take shape in various molds. Different types of melting equipment are available, each with their own unique characteristics and benefits, so let's take a deeper look into each.
Induction Melters
Induction melters utilize electromagnetic fields to generate heat directly in the metal, providing a precise means of melting. This method is favored for its ability to achieve consistent temperatures without direct flames. One of the most notable benefits of induction melters is their energy efficiency, which allows for a quick heating process without unnecessary heat loss.
Their compact design makes them a convenient choice for workshops with limited space, but they do tend to come with a higher price tag compared to other options. Though they may be an investment, the longevity and level of control they offer can easily outweigh the initial costs.
Torch Melting
Torch melting is a more traditional approach and involves using a torch to apply heat directly to the metal. Jewelers often appreciate this method for its simplicity and versatility. One of the key characteristics of torch melting is the jewelers' ability to control the flame directly, allowing for adjustments on the fly.
However, the precision can be more challenging compared to other forms of melting equipment. Nonetheless, it provides a valuable option for those who prefer a hands-on approach or who work on small-scale projects. The downside, of course, is the potential for uneven heating, which can lead to compromised results.
Kilns
Kilns play an essential role not just in melting but also for firing and hardening certain materials. They provide a controlled environment to achieve specific temperatures and can accommodate larger batches of metal as well. A kiln can handle multiple projects at once, making it a favorite for jewelry makers who are managing large runs of casting.
They require more setup time and may take longer to reach optimal temperatures, but the results often justify the effort. Kilns are particularly useful when working with materials that need extended heating times, making them indispensable in many jewelry workshops.
Casting Molds and Frames
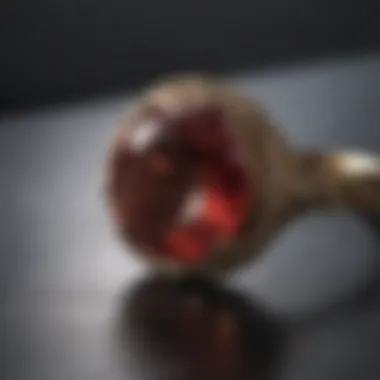
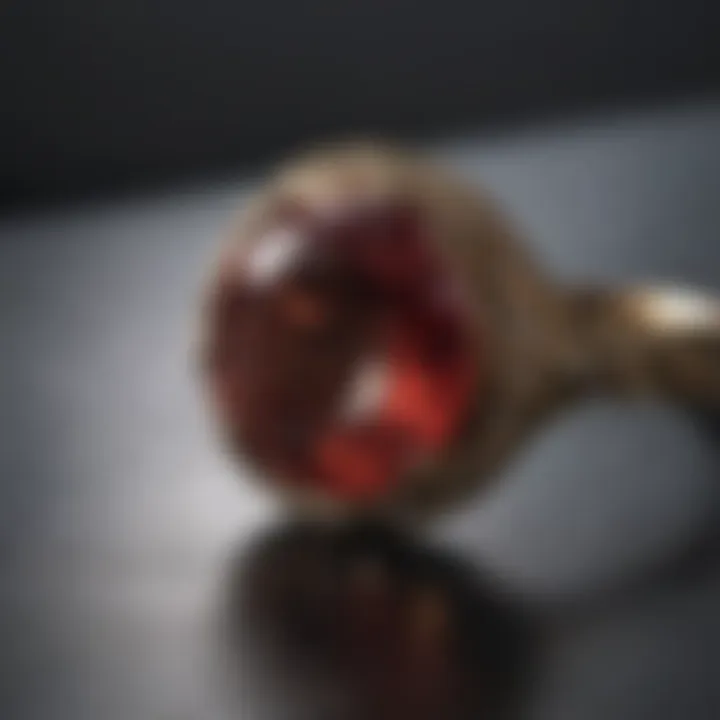
Casting molds and frames are equally critical, as they shape the hot metal into the desired design. Understanding the different types of molds available can profoundly influence the efficiency and creativity of the casting process.
Silicone Molds
Silicone molds are incredibly popular in jewelry casting. They offer great flexibility and allow for easy removal of the final product without risking damage. Their ability to capture intricate details is impressive, making them an excellent choice for any level of jeweler. However, they may have lower heat resistance compared to metal molds and can wear out faster, necessitating replacement over time.
Metal Molds
Metal molds are robust and can withstand high temperatures, making them suitable for various metals. They typically last longer than silicone molds and provide a smooth finish to the final piece. On the flip side, they can be heavier and more challenging to work with.
Shell Molds
Shell molds combine the advantages of both silicone and metal. They are created by layering a ceramic material over a prepared wax model, allowing for excellent detail reproduction and durability. The infamous heat retention of shell molds results in superior casting conditions, although it can be more labor-intensive and time-consuming to create.
Wax Products
In the casting process, wax acts as a vital model for lost wax casting techniques. The different types of wax products each contribute uniquely to the creation process, and selecting the right kind of wax can make all the difference.
Modeling Wax
Modeling wax is used for creating the original forms that will later be cast. Its key characteristic is malleability, allowing jewelers to carve and shape intricate designs easily. The downside is that it may not retain fine details if subjected to high temperatures too quickly, which can impact the final cast.
Injection Wax
Injection wax is employed in precise and intricate designs. By using a mold, it can replicate details minutely, which is a clear advantage when aiming for perfection. However, it usually requires certain equipment for injection, making it less accessible for all jewelers.
Carving Wax
Carving wax is mostly used for creating models directly. Its versatility allows for both carving and shaping, which can be particularly useful. The downside is that it may not hold up as well under high heat, straining the casting process.
By understanding these essential jewelry casting supplies, jewelers can make informed decisions that not only streamline their processes but also uplift their craftsmanship, paving the way for creativity and innovation in the field.
Types of Jewelry Casting Techniques
The world of jewelry casting involves a variety of techniques that allow artisans to create unique and intricate designs. Understanding these methods is crucial not only for those engaged in jewelry-making but also for enthusiasts who appreciate the artistry behind each piece. Each casting technique brings with it specific benefits, challenges, and applications, giving jewelers the flexibility to express their creativity while ensuring quality in the final product.
Lost Wax Casting
Lost wax casting, also known as investment casting, is one of the most traditional as well as popular methods used in jewelry making. This technique involves creating a model of the jewelry piece in wax. Once the model is crafted, it's covered with a heat-resistant material that hardens into a mold. The process then involves melting away the wax, leaving a cavity where metal can be poured.
Importance of Lost Wax Casting:
- Precision and Detail: This method allows for high levels of detail, making it ideal for complex designs like filigree or intricate patterns.
- Versatility: Jewelers can utilize lost wax casting to create pieces in a variety of metals, including gold, silver, and bronze.
- Repeatability: Once a mold is created, multiple copies can be made, which is a huge advantage for mass production.
"In jewelry making, lost wax casting isn’t just a method; it's a bridge connecting ancient traditions with modern artistry."
However, it's also important to consider potential drawbacks. The initial labor and time required for creating a wax model can be extensive. Additionally, this technique can involve a steep learning curve, as mastering the mold-making and pouring process requires practice and skill.
Die Casting
Die casting is another prominent technique used in jewelry production. Unlike lost wax casting, die casting entails forcing molten metal into a reusable mold, which is often machined precisely to hold the intended design. This method is favored for its speed and efficiency, making it suitable for high-volume production.
Key Benefits of Die Casting:
- Speed of Production: Ideal for producing large quantities quickly. Once the molds are made, the process can be quite rapid.
- Cost-Effectiveness: When producing items on a large scale, die casting can be more economical compared to individual investment casting.
- Strength and Durability: The resulting pieces tend to have a robust structure, valuable for functional jewelry pieces that see daily wear.
However, die casting may not be as effective for highly detailed designs, since the molds are more generalized compared to wax models. Jewelers need to balance between detail and production needs when choosing this method, which can sometimes place restrictions on artistic expression.
Centrifugal Casting
Centrifugal casting means using centrifugal force to direct molten metal into a mold. This is particularly useful for crafting intricate pieces and can create strong, durable designs due to the even distribution of metal under force. It's often employed for both large volume productions and unique, artistic items.
Benefits of Centrifugal Casting:
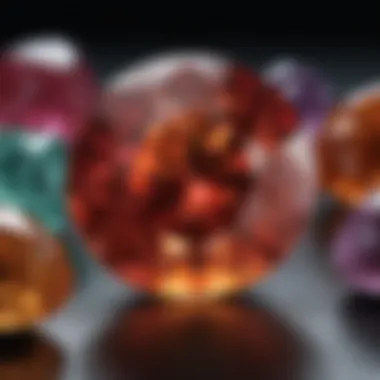
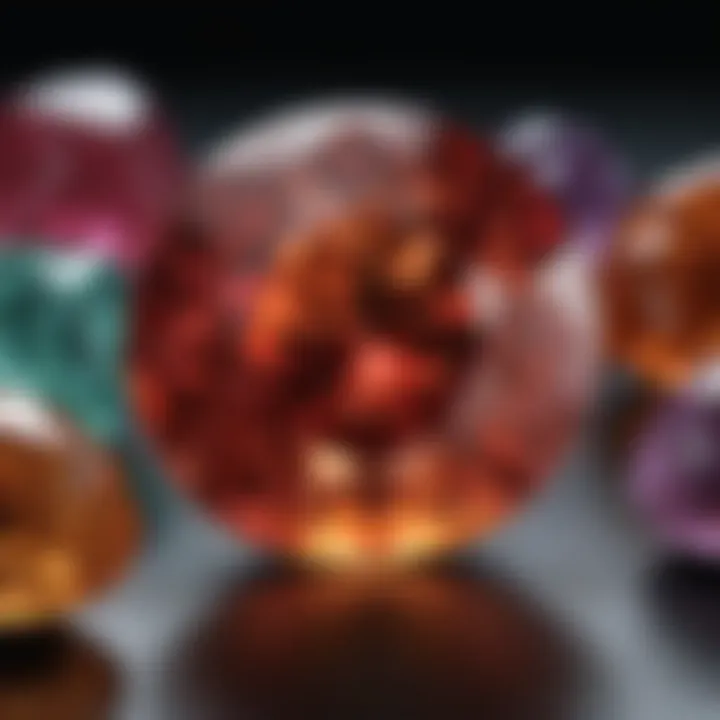
- Enhanced Filling of Molds: The force helps to fill molds more completely, minimizing air bubbles and ensuring better finish.
- Perfect for Intricate Designs: This method is well-suited for pieces requiring exceptional detail, making it a choice for many fine jewelers.
- Time Efficiency: It allows for faster production times than traditional pouring methods while still producing high-quality results.
However, centrifugal casting does have its own set of challenges, including the need for precise control over the speed and technique. Any misstep in the process can lead to flaws in the final piece, requiring jewelers to have a steady hand and keen eye.
In summary, the choice of casting technique affects not only the quality of the jewelry but also the creative possibilities available to the jeweler. Each method—lost wax casting, die casting, and centrifugal casting—offers distinct advantages and considerations, serving different needs and artistic goals. Understanding these techniques can greatly enhance both the craft and appreciation of jewelry making.
Choosing Quality Casting Supplies
When it comes to jewelry making, the quality of your casting supplies can be the golden thread that ties together a well-crafted piece or results in a disappointing failure. Selecting high-grade materials not only ensures a polished finish but also affects the durability, aesthetic appeal, and even the safety of the final product. Poor quality supplies can lead to disaster, from warped designs to allergic reactions in wearers. Therefore, it's imperative to dig a little deeper and understand the ins and outs of choosing quality casting supplies.
Identifying Trusted Suppliers
Finding reliable suppliers can be a bit of a head-scratcher. The market is riddled with options, and truth be told, not all suppliers have your best interests at heart. Start by looking for suppliers who specialize specifically in casting supplies and have a robust track record. Check reviews not just on their website, but also on platforms like Reddit, where jewelers gather to spill the tea on their experiences.
Some factors to consider include:
- Reputation: A supplier known for quality is generally a safer bet.
- Recommendations: Seek advice from fellow jewelers or gemstone enthusiasts to find suppliers who've built a solid reputation.
- Certification: Look for suppliers who are transparent about the standards and certifications their materials meet.
By making informed choices, you minimize the risk associated with subpar materials. It's like choosing between a hand-forged tool versus a mass-produced gadget — the difference often manifests in the final piece.
Material Composition Standards
The various materials you'll use in casting — metals, waxes, and molds — each come with their own set of standards. Understanding these is crucial, especially in today’s market, where shortcuts are the name of the game for some suppliers. A solid grounding in material composition can be the difference between a lusterless lump and a dazzling jewel.
Key standards to keep in mind:
- Purity Levels: For metals like gold or silver, check for hallmarking that indicates purity. For example, 18K gold should contain 75% pure gold.
- Additives: Sometimes, cheaper metals are mixed with other elements that can affect skin reactions. Investigate what’s in the mix to avoid trouble down the line.
- Wax Quality: Not all wax is created equal. High-quality waxes will have specific melting points and workability characteristics that can greatly influence your sculpting and final casting.
Constantly educating yourself about these standards can put you a step ahead and can save you heartache and expense.
Sustainability Considerations
In an age where consumers are increasingly mindful of their choices, sustainability holds significant weight. Sustainable practices aren't just good for the planet; they can also enhance your brand's image and attract a conscientious customer base.
When evaluating suppliers, consider these sustainability factors:
- Material Sourcing: Check if the supplier sources materials from responsible and ethical mines. Conflict minerals can turn your masterpiece into a controversial artifact.
- Recyclability: Some suppliers offer recycled metals or materials that reduce the environmental impact. Using what’s already out there instead of starting from scratch can shift the balance in your favor.
- Supplier Practices: Investigate whether suppliers practice eco-friendly procedures in their operations, such as reducing waste and energy usage.
In today's market, consumers gravitate toward transparency. Providing clarity in your material choices resonates well with buyers and creates a deeper connection to your work.
"In choosing quality casting supplies, you’re not just making a purchasing decision; you’re crafting an entire narrative that will echo through your creations."
By taking the time to choose wisely, you’re not only positioning yourself as a craftsman of quality but also as a responsible creator in the intricate world of jewelry casting. It’s a step that enriches not just your artistry but also enriches the community at large.
Innovations in Jewelry Casting Supplies
As the jewelry industry continues to evolve, innovation becomes a vital factor in enhancing the quality and efficiency of jewelry casting supplies. In recent years, the blending of technology and artistry has brought about significant advancements that deserve attention. Not only do these innovations improve productivity, but they also elevate the entire jewelry-making experience. For both seasoned artisans and aspiring jewelers, keeping an eye on emerging trends can open doors to superior craftsmanship and more sustainable practices, making them a critical focus area of this article.
Emerging Technologies
Technology is reshaping the landscape of jewelry casting in fascinating ways. For example, 3D printing has gained traction for its ability to create precise models that traditional methods may struggle with. This advancement allows jewelers to prototype designs quickly and efficiently without wasting valuable materials.
Moreover, computer-aided design (CAD) software has become a go-to tool for many designers. It enables them to visualize intricate designs before they cast, ensuring that what they produce aligns perfectly with their vision. Combining CAD with CNC (Computer Numerical Control) machinery further streamlines the casting process, allowing for intricate designs with minimal manual labor.
Another noteworthy advancement includes the development of advanced alloys and casting resins which can now incorporate unique properties such as increased strength, reduced weight, or even hypoallergenic characteristics. As such, these materials provide jewelers with the flexibility to create diverse designs while meeting consumer demands for quality and safety.
Eco-Friendly Materials
With increased awareness about environmental impacts, the jewelry-making milieu has shifted toward more sustainable practices. One of the foremost innovations involves the use of eco-friendly materials. The market sees a growing availability of recycled metals. Using these metals reduces the need for mining, thus lessening the ecological footprint of the jewelry-making process.
In addition to recycled metals, biodegradable wax has emerged as a sustainable alternative for traditional casting workflows. Many manufacturers now offer wax that breaks down naturally, providing a less harmful way to create intricate designs.
"Using eco-friendly materials is not just a trend; it's a necessity for the future of our planet."
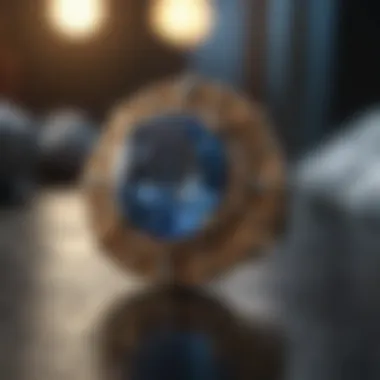
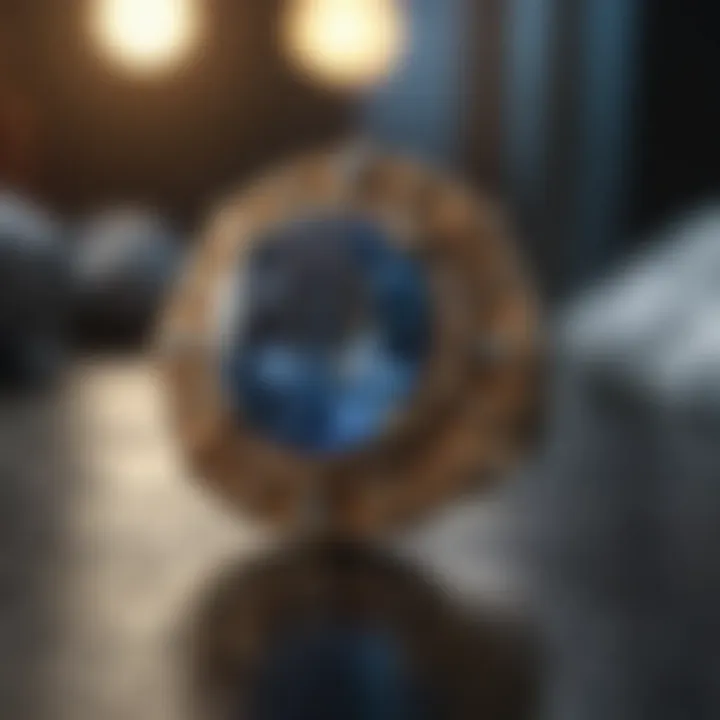
Furthermore, some casting techniques are now leveraging plant-based resins, which can serve as an alternative to synthetic resins that release harmful pollutants during production. This shift not only meets the demands for more eco-conscious products but also aligns with growing consumer preferences for sustainability in their purchases.
Overall, innovation in jewelry casting supplies paints a picture of a forward-thinking industry that embraces change. By tapping into emerging technologies and choosing eco-friendly materials, jewelers can craft stunning pieces that resonate with integrity and responsibility, fostering a connection between art, industry, and the environment.
Application of Casting Supplies in Jewelry Design
Casting supplies play a pivotal role in jewelry design, shaping not just the final piece but also the creative process behind it. With the right materials and tools, jewelers can mold their imaginative visions into tangible works of art. Each supply type—from molds to wax types—opens new avenues in the design, pushing the boundaries of what’s possible. Here’s a closer look at how casting supplies influence two critical aspects of jewelry creation: integrating gemstones and crafting unique designs.
Integrating Gemstones
When it comes to integrating gemstones into jewelry, the choice of casting supplies can greatly influence the outcome. The casting method determines how securely a gemstone is set into its metal framework. For instance, utilizing lost wax casting allows for intricate designs that can hold gemstones snugly, without compromising on aesthetics. This method offers a seamless look; the wax model can be made to exactly fit the stone, ensuring both beauty and stability.
Considerations for Integrating Gemstones:
- Type of Mounting: Different casting techniques lead to various types of mounting, such as bezel settings that can cradle the stone securely.
- Durability of the Metal: The selected metal's hardness can affect the gemstone's safety. Softer metals might bend over time, risking the stone's setting.
- Design Complexity: Some gemstones, especially larger ones, may require specialized molds to maintain their integrity during casting. For instance, if a large opal is set in a piece, it's crucial to use robust materials during the casting process to avoid damage to both the stone and the design itself.
"Incorporating gemstones effectively means starting from a solid foundation—your choice in casting supplies is that foundation."
Creating Unique Designs
Creating unique designs is where the magic of casting supplies truly shines. Jewelers can break free from traditional molds and venture into uncharted design territory. With supplies like flexible silicone molds, one can experiment with shapes and patterns that would be impossible with rigid options. The flexibility allows designers to create pieces that reflect personal style or thematic influences, thus setting their work apart in a crowded market.
Key Elements to Consider for Unique Designs:
- Material Selection: Different materials—such as resin or metal—can be combined in the casting process to give a mixed-media effect.
- Customization Opportunities: Many casting supplies allow for designs to be individualized. Jewelers can create limited-edition pieces tailored to specific clients.
- Environmental Impact: Today, there's an increasing emphasis on eco-friendly practices. Unique designs can be made from sustainable or recycled materials, appealing to environmentally-conscious consumers.
In essence, integrating the right casting supplies can foster an environment ripe for creativity in jewelry design. The ability to merge gemstones with distinct designs not only enhances the artistry of the piece but also elevates the wearer's experience. The correct approach can bolster one's portfolio, attract discerning clients, and ultimately lead to greater success in the ever-evolving landscape of jewelry making.
Maintenance of Casting Tools and Supplies
To create dazzling jewelry pieces, one needs not just skill, but also high-quality tools and supplies. Maintenance of casting tools and supplies is pivotal in ensuring the longevity and efficiency of the equipment. When you think about it, every time a jeweler steps into their workshop, it’s like an artist preparing their canvas. The tools should shine, with every part functioning smoothly to achieve that perfect finish.
Not only does regular maintenance enhance the life span of tools, but it also prevents mishaps that might sabotage a beautiful piece of jewelry in the making. A poorly maintained tool can lead to defects, which could be anything from rough edges to unexpected breaks during casting. By caring for these tools, artisans ensure they get the best possible results every time.
Cleaning Techniques
Cleaning techniques can be likened to the rituals in a chef's kitchen; they're essential for achieving pristine results. Here are some important points to consider when cleaning casting tools:
- Frequency: Set a routine — after each use or a few times a week, depending upon how often you’re working. This avoids a buildup of residues, dirt, and wax.
- Materials: Different tools require different cleaning agents. For instance, metal molds might need a mild detergent and warm water, while silicones often just require a gentle wipe with a damp cloth. Using harsh chemicals can damage the tools, leading to costly replacements.
- Technique: Use soft brushes or cloths to scrub away any remnants without scratching the surface. For waxy residues, warm soapy water often does wonders.
"A clean tool is a happy tool. It takes care of you and your jewelry in return."
Storage Recommendations
The way you store your casting tools is just as important as how you clean them. Proper storage can keep tools functional and in excellent condition. Here are some recommendations to consider:
- Dry Environment: Ensure that tools are stored in a dry place. Humidity can cause metal tools to corrode. A desiccant or silica gel packs can be a helpful addition to your storage solutions.
- Organized Space: Use racks or dedicated boxes for different types of tools. This not only helps in finding what you need but also reduces the chances of damage from tools bumping into each other or getting lost.
- Gentleness: For particularly delicate items, such as molds, consider wrapping them in cloth or placing them in cushioned containers.
By incorporating thoughtful cleaning techniques and proper storage recommendations, you safeguard your investments and enhance your jewelry-making endeavors. It's a small effort that yields significant rewards down the line.
Culmination
The conclusion of this comprehensive exploration into jewelry casting supplies serves as a reflective opportunity to evaluate the significance of each discussed aspect. Jewelry casting is not merely a technical endeavor; it requires an amalgamation of skill, creativity, and an understanding of materials.
Future Directions in Jewelry Casting
As we gaze into the future of jewelry casting, the road ahead seems vibrant with potential. Innovations in technology continue to mold the landscape. Techniques like 3D printing are redefining how molds and models are created, allowing for intricacies that traditional methods simply cannot achieve. The integration of smart materials, which respond to environmental changes, is also gaining traction. This presents not only an opportunity for enhanced functionality but invites further creativity in design too.
Moreover, as sustainability claims a rightful seat at the table of many industries, the jewelry sector must also adapt. Expect to see increased use of recycled metals and ethical sourcing of gemstones becoming the norm rather than the exception. As consumers become more conscientious about their purchases, jewelers will need to be proactive about communicating their efforts in these areas.
The future may be a fusion of artistry and innovation, where both can thrive harmoniously.
Final Thoughts on Craftsmanship
In the end, craftsmanship in jewelry making transcends the mere act of joining materials. It's a profound dance between tradition and innovation, discipline and inspiration. Jewelers must understand that each piece they create carries a narrative, often drawing from personal experiences or cultural significances. The attention paid to tools and supplies not only enhances the technical quality of a piece but also reflects the mindset and values of the artist behind it.
A jeweler's ability to balance the use of cutting-edge technology with traditional techniques often dictates their success in this competitive field. By embracing both, artisans can push boundaries while respecting the age-old practices that have shaped the craft. A commitment to lifelong learning and exploration is key for those looking to leave an indelible mark in the world of jewelry casting.
In summary, understanding the multifaceted nature of jewelry casting supplies and techniques leads to a richer, more informed approach to craftsmanship and design. As the jewelry landscape grows and changes, so too will the need for those who engage with it to adapt and thrive.